生産計画業務のよくある課題〜Asprova社が綴る〜
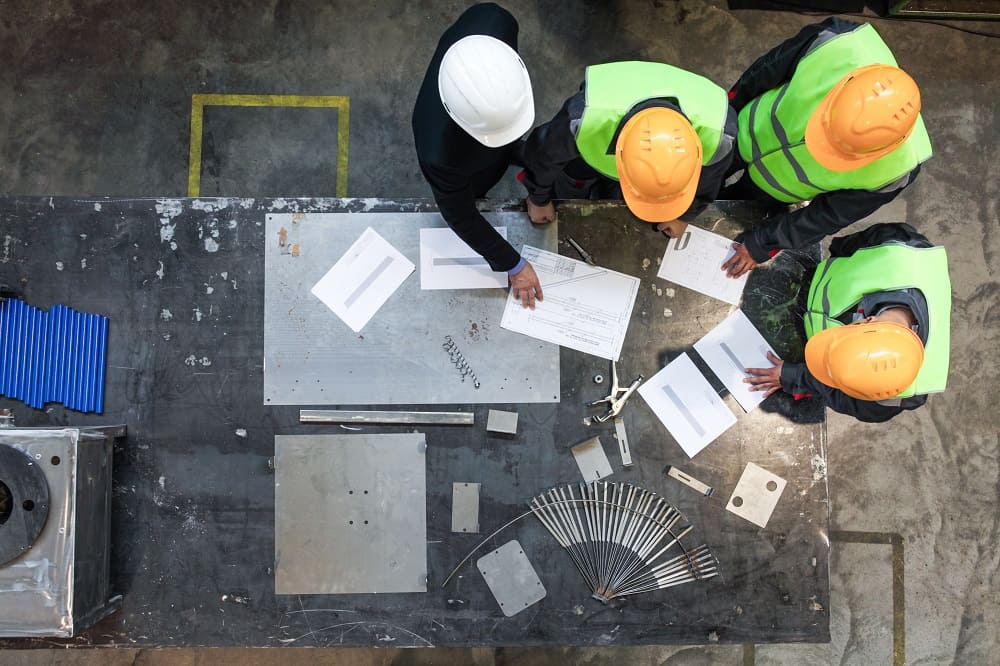
弊社は生産スケジューラAsprovaの開発元になります。
これまでに数百社の生産計画業務を拝見し、担当者の皆さまと会話させて頂きました。
業種や工程によってお困り事が違うところは当然ありますが、一方で皆さま共通の課題を抱えておられます。
その課題を幾つかご紹介したいと思います。
生産スケジューラ(生産計画システム)に関する資料をダウンロードできます
1.欠品せずに在庫削減したい
生産管理のご担当者様に在庫についてインタビューさせて頂きますと、以下のような課題があるとお答えされることが多いです。
- 完成品、半製品、原料のどれも在庫が多く、管理費がかさむ
- 急な注文変更に対応できるように在庫を持っておかないといけない
- 仕掛かり在庫が山積みになっている
- 死蔵品が倉庫に山のようにある
在庫は、決算書に棚卸資産として表れ、キャッシュフローが悪いと評価されて株価に影響します。在庫を少なくすることで、①会社の借入金を減らす効果②置き場所を少なくして工場の敷地を有効活用でき、在庫保管コスト低下させる効果、などを期待できます。
在庫管理の手法としては、発注点方式、カンバン方式、などがあり、これらで管理できる品目があります。但し、調達リードタイムが長い品目、需要変動が激しい品目、高額な品目などは、これらの方式で管理し難いため解決方法を別途考える必要があります。
では、減ったら作るのではなく、予測をもとに生産したらどうでしょうか。予測が当たれば、生産計画も正確になり、「在庫ゼロ、欠品ゼロ」にできるはずです。しかし、会社で販売している製品は、数千種類あり、売れ行きを予測するのは難しく、季節、地域、天候、景気、など様々な外部環境に左右されます。もし、予測が外れて欠品すれば売上を逸することになります。
多く売れると見込んで生産すれば売れ行きが悪いと死蔵品になり、ゆくゆくは大幅値引きか、最悪廃棄になってしまいます。顧客の購買行動は正確に予測できず、需要予測を100%確実に行うことはできません。
2.納期厳守したい
受注生産品(Make-To-Order)では、顧客からの希望納期に対して、回答納期をこたえます。
極力、顧客の希望納期に沿うようにしたいものです。場合によっては希望納期に沿えないこともあります。
最終的に契約が締結されるときに納期が確定します。この確定納期には絶対に遅れてはなりません。
そういった状況下にある生産管理のご担当者様に、納期についてインタビューさせて頂いたところ、以下のような回答を頂きました。
- 納期の要求が厳しくなっているが、対応できない
- 特急オーダや納期変更に計画の変更が追い付かない
- 特急オーダなどに対応するには、在庫を保持するしかない
- 計画を確認せずに無理な注文を受けて、納期遅れになる
- 計画担当者に確認しないと、計画が分からず、正しい納期回答ができない
- 納期遅れのペナルティを避けたい
- 納期遅れ件数が減らないので、お客様の期待が上がらない
- 誰でも納期回答できるようにしたい
- 声が大きい影響力のある営業担当者の注文ばかり優先され、他の注文がいつも納期ギリギリになる
- 納期厳守のため残業してコスト高になる
- 納期遅れは、会社の信用失墜であり、会社の存続に影響する
1.と2.の課題認識から在庫と納期の両立は大変に難しいことがわかります。
それ故、製造業様において生産計画業務は大変重要な役割を担っていると思います。
3.変化対応力を向上したい
在庫過多、欠品、納期遅れは、極力避けたいですが、生産過程では予期せぬ事が次々に起こります。
- 突然、作業者が病欠した
- 設備が故障した
- 金型が破損した
- 部品の入庫が遅れた
- 不良品が発生した
- オーダ数量が増えた、減った
- オーダ納期が変更になった
- オーダがキャンセルされた
在庫過多、欠品や納期遅れを起こさないようにするためには、残業や休日出勤するなどして、これら変化に対処する必要があります。自動車の組立では、一つの部品が遅れただけでも、組立が不可能になります。よって、絶対に納期遅れは避けたいところです。このような場合は、総務部の人員が製造現場で作業に当たることがあります。
変化に追随する必要がある中で、人手によるExcelで差立てを行っている場合はどうでしょうか。長時間かけて、やっと作成した詳細スケジュールが、一つの要因、例えば、特急オーダが入ってきた時に、全体にどんな影響があるのか、他のオーダが納期遅れにならないか、残業、休日出勤が必要にならないか。人手によるExcelでは、タイムリーに再度詳細スケジュールを作成し直すことは不可能に近いです。
4.リードタイムを短縮したい
製造業の経営者の皆さまに、お持ちの課題は何かとインタビューさせて頂きますと「リードタイム短縮」が多く挙がります。それほどにリードタイム短縮の重要性は認識されています。生産リードタイムが短いと、以下の4つの効果があります。
- 納入リードタイム短縮
- 製品・仕掛品・原料在庫の削減
- モデルチェンジ時の死蔵品の削減
- オーダ変更への対応力向上
リードタイム短縮の効果は、リードタイムが究極的にゼロに近づいた状態を想像するとよくわかると思います。リードタイムがゼロであれば、納期直前に購買・生産を開始すればよく、在庫=0、納期遵守率=100%になります。実際には、リードタイムがゼロになることはありません。しかし、リードタイムが短ければ短いほど在庫=0、納期遵守率=100%の状態に近づくことは確かです。
しかし、実際にリードタイムが長くなるのはどんな原因によるのでしょうか。「現場の都合で、まとめ生産している」、「滞留した仕掛品が忘れられて放置されたままになっている」、「MRPで計算した投入日時が早過ぎる 」などがあります。リードタイムの殆どは実は滞留時間であるともよく聞きます。
リードタイムを短縮する方法としては、例えば、セル生産のように多工程を一人で行うことによって、1工程にし、且つ、リードタイム短縮を図ることが考えられます。多工程を1工程にする工夫は重要と思います。工程数が少ない場合は、まだ、リードタイムをコントロールしやすいと思います。需要変動が激しい場合は、安全在庫では対処することが難しいです。安全在庫は未来の不確定性の標準偏差に比例した安全在庫量になるため、需要増には対処していますが、需要減のときに大量の在庫が発生しやすい傾向があります。
いずれも難しい課題であり、解決などない永遠に続く課題とも思いますが、生産スケジューラAsprovaが改善の一助となる可能性はあります。生産スケジューラAsprovaの特徴に ついては「生産スケジューラ(生産計画システム)とMRPの特徴」でご説明しておりますので、是非ご確認ください。
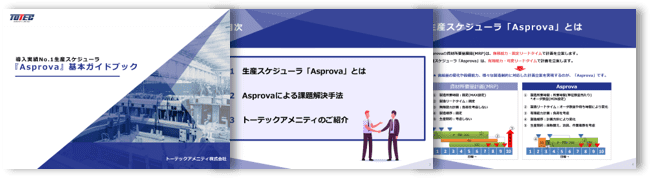
生産スケジューラ『Asprova』
基本ガイドブック
お困りごとがありましたら、お気軽にお問合せください。