生産スケジューラ(生産計画システム)とMRPの特徴
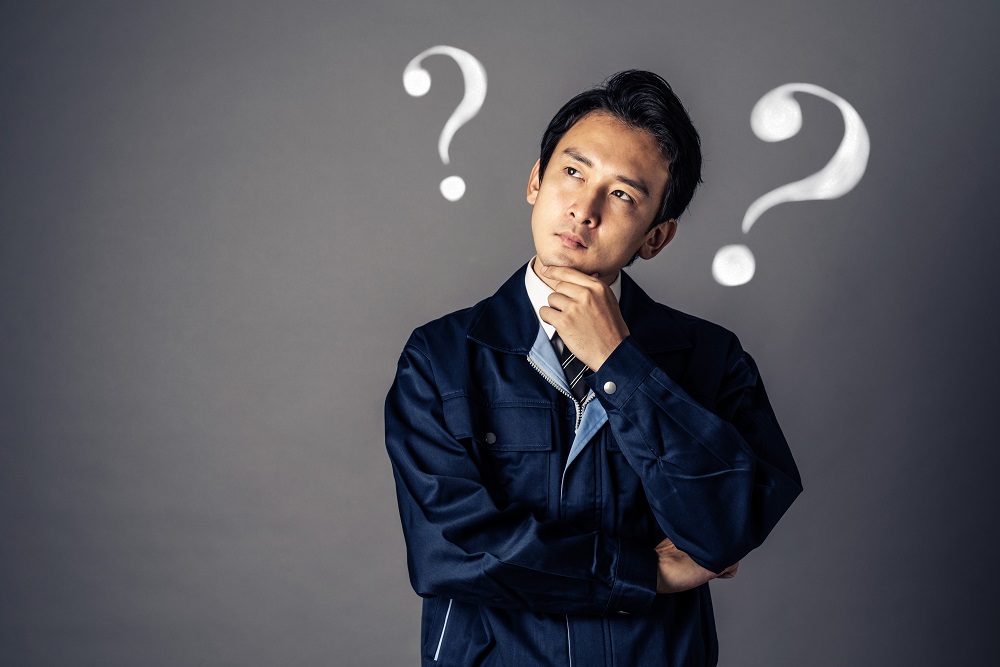
連載テーマ「生産スケジューラ(生産計画システム)導入を"成功"に導く秘訣」
- Vol.1 生産計画とは〜生産計画業務と生産計画の種類について〜
- Vol.2 生産スケジューラ(生産計画システム)とMRPの特徴
- Vol.3 生産スケジューラ(生産計画システム)の導入手順No.1
- Vol.4 生産スケジューラ(生産計画システム)導入をスムーズに進める為に準備するもの
- Vol.5 ERPと生産スケジューラ(生産計画システム)のデータ連携
- Vol.6 生産スケジューラ(生産計画システム)を利用した計画立案方針について
- Vol.7 【事例紹介】生産スケジューラ(生産計画システム)を利用したネック工程最適化
- Vol.8 【事例紹介】生産スケジューラ(生産計画システム)を利用した業務改善
- Vol.9 生産スケジューラ(生産計画システム)導入手順No.2
生産計画をシステムで立案するときに、生産スケジューラ(生産計画システム)以外を利用する場合はMRP(Material Requirements Planning)を利用されるケースが多いのではないでしょうか。
今回は、MRPと生産スケジューラ(生産計画システム)の特徴について説明していきます。
生産スケジューラ(生産計画システム)に関する資料をダウンロードできます
所要量展開・MRPとは
需要(受注や内示・販売予測や、後工程の消費予定)から製造LT(リードタイム)、
製造ロットを加味して各日の必要量を計算させます。
簡単な例を交えて説明していきます。

図1:品番情報
上記の図1は所要量展開を実施するのに必要な情報を表しております。
■品番情報の項目
品番:品目を表す番号となります。
安全在庫:所要量計算を行うにあたり、当在庫数量を割らないように計算します。
製造ロット:製造を行う時に、この数量の倍数になるように計算します。
材料品番:品番を製造するために必要な材料品番となります。
この情報を利用した所要量計算結果を図2から説明していきます。
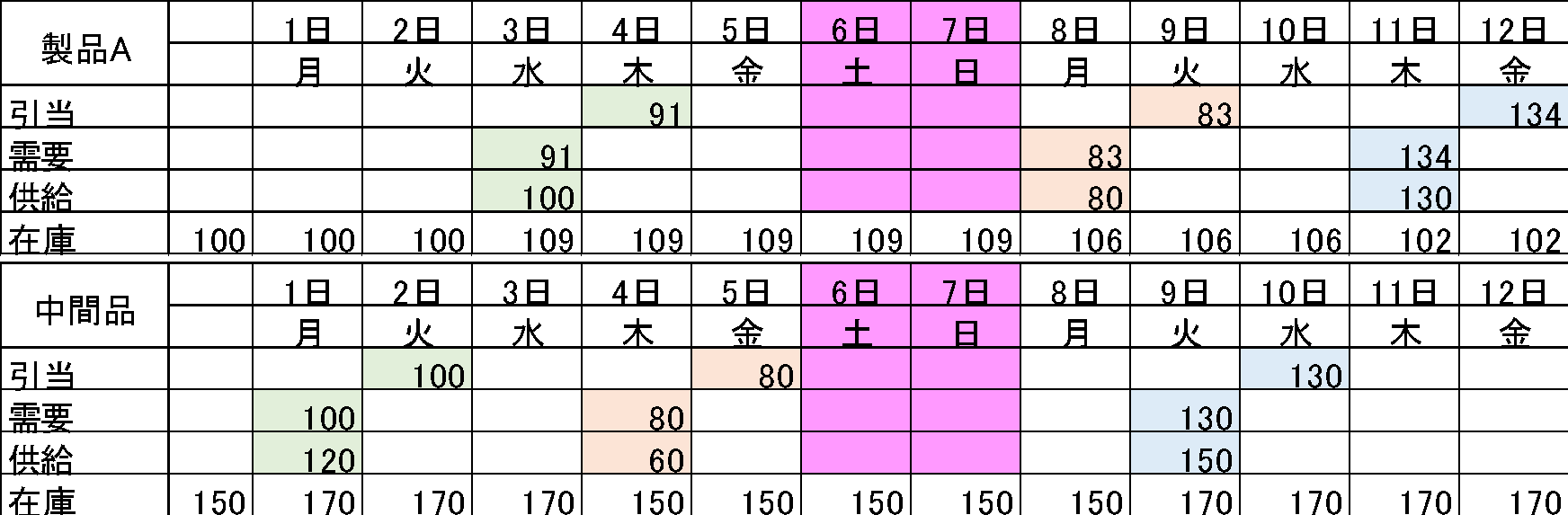
図2:所要量計算結果
■所要量計算結果の項目
引当:受注や内示、後工程の消費予定など、消費される数量を表します。
需要:配送や物の移動などで引当にかかるまでの時間をずらした数量を表します。
※多くのシステムでは、配送LTなど移動を表す時間を品目情報に設定致します。
図2では1日を設定してある想定です。
供給:品目情報の製造ロットの倍数で製造必要量を求めます。
※製造LTを品目情報に持たせて、材料は設定された日数前に引当の所要量が 計算されます。
図2では2日を設定してある想定です。
在庫:各日終わり在庫量を表しています。
計算式は「前日在庫 + 供給 - 需要」となります。
製品Aの引当から設定に従って、中間品までの計算を行っております。
実工場では中間品は複数の製品で利用される事が存在しております。
ご説明した図2の情報へ製品Bを追加した例を説明していきます。
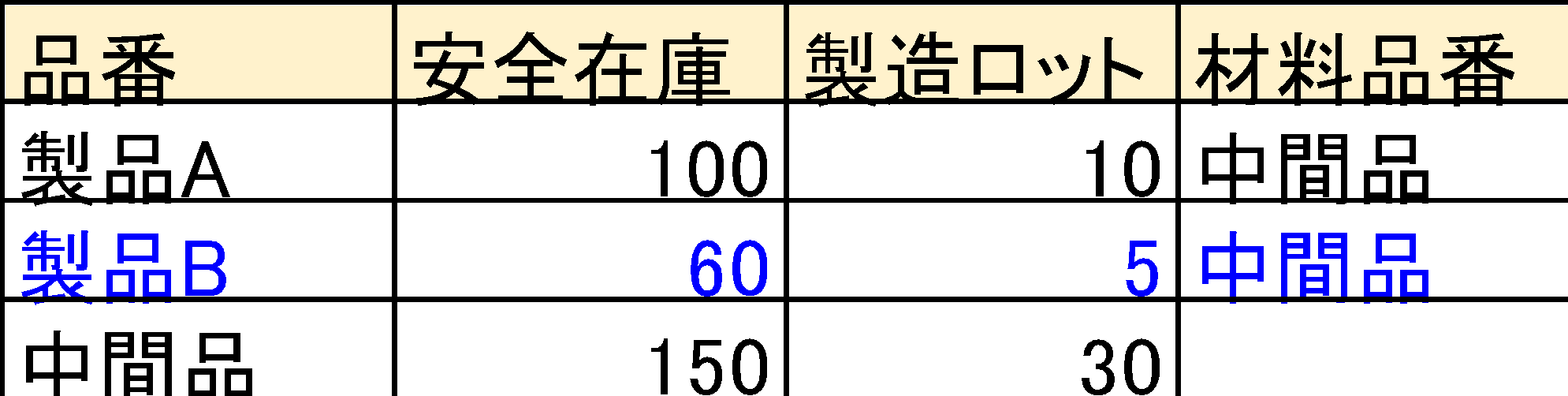
図3:品番情報(製品B追加)
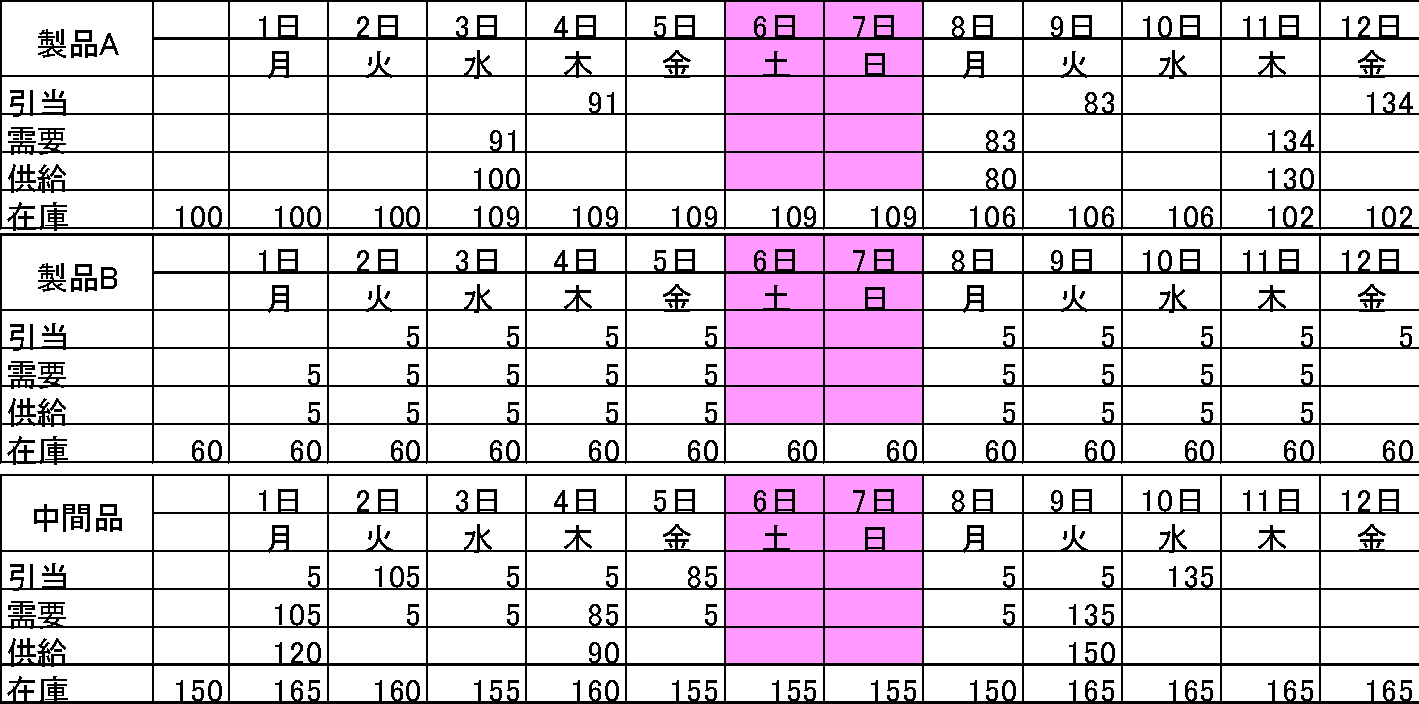
図4:所要量計算結果(製品B追加)
図4の中間品は製品Aへの引当と製品Bへの引当の双方を加味して計算を行っております。
実際の工場では親子(製品Aと中間品)だけの関係ではなく、[親][子] [孫] [ひ孫]と構成は多岐に渡ります。また、製品Aと製品Bのような共通部品も多く存在しております。
それをひとまとめに必要量を計算させることができるのが所要量計算処理となります。
生産スケジューラ(生産計画システム)
「1.所要量計算」の図4結果を生産スケジューラ(生産計画システム)で表した場合にどのようになるか説明していきます。
生産スケジューラ(生産計画システム)は
・設備制約を加味して有限で割り付ける
・前後工程を紐付けて計画する
の2つを実現しながら計画立案するシステムになります。

図5:生産スケジューラ(生産計画システム)に設定する稼働時間
図5に示した需要量を満たす製造を”有限能力”で生産スケジューラ(生産計画システム)へ割り付けていきます。各設備(この例ではライン①)に製造できる稼働時間を設定していきます。
Point:稼働時間は製造が可能な時間を設定します。人は勤務時間に合わせますが、設備は昼休みも稼働している場合は、休みではなく稼働時間として設定致します。
生産スケジューラ(生産計画システム)に制約・要望を加えていきます。
■制約例
・製品Aと製品Bは同じライン①で製造する。
・1日の製造は80個までである。
■要望例
・製品Bは需要がある日に製造したい。
・製品Aは大きな需要を製品Bの製造する合間に分割して入れたい。
制約のみを取り入れて、所要量計算結果を入れると図6のようになります。
※青バー:製品A、オレンジバー:製品B

図6:所要量計算結果を生産スケジューラ(生産計画システム)に割り付ける。
ここで結果は要望例が実現できない結果になっております。
なぜなら『生産スケジューラでは作成した作業バー単位に有限能力で割り付ける』動作を致します。したがって、製品Aの作業バーはMRPと同じ結果の長さにしてしまうと、連続して製造する計画になってしまいます。
○連続製造させないためには
生産スケジューラ(生産計画システム)で細かく計画するためには、この作業バーを細かく分断する必要があります。
分断させる方法は、いくつかありますが代表的な内容として【最大ロット】を設定する方法があります。
最大ロット:所要計算で求めた結果を特定の数量で作業バーを分裂させる機能
MRPは最低ロットなど所要がある場合にまとめて製造する量を定義致しますが生産スケジューラ(生産計画システム)では、最低ロットだけではなく、最大ロットを決める必要があります。
Point:製造ロットは細かく設定すれば、データ量が増えてしまうため、収容数など一定の大きさを定義することが一般的です。
導入前に各工程の最大ロットを検討しておいてください。
図6の結果に最大ロット「10」を設定し要件例を加味して並べると以下の図7のように計画が立案されます。
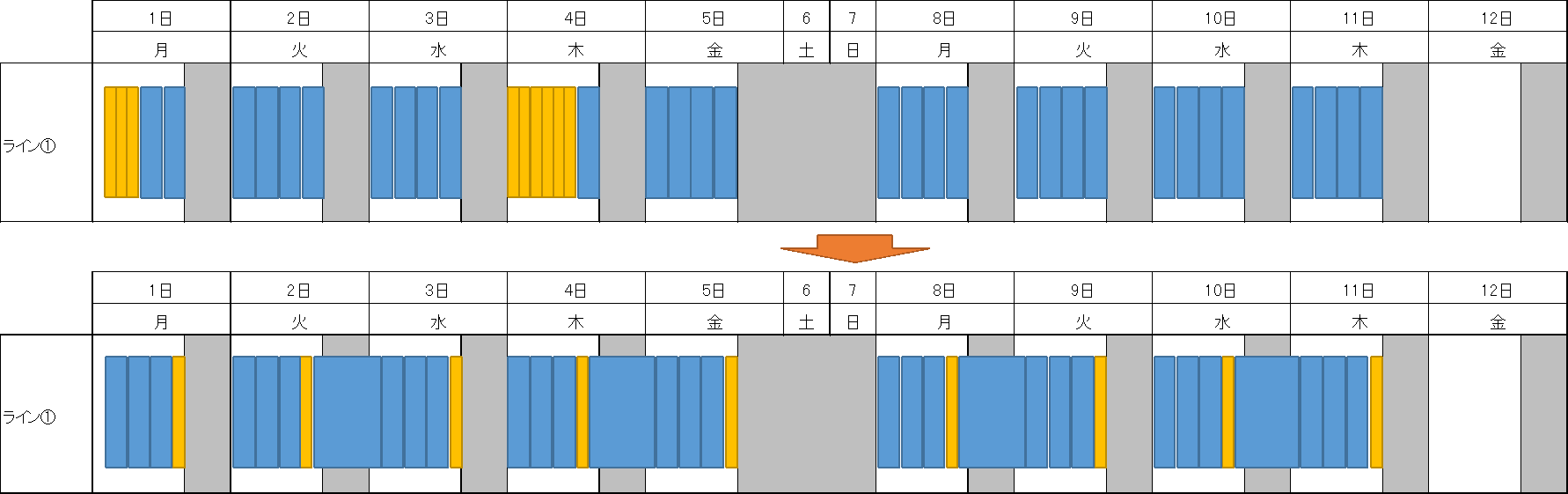
図7:製品Aに最大ロット「10」を設定した結果
この結果により制約・要望の双方を満たした計画が立案できます。
ただし、データが細かくなってしまいますので、【計画調整】を行うのが難しくなる場合があります。(製造を分割する単位が細かいほどデータ量が増大します)
※前後工程がある場合は、そちらも制約として動作するため、全体を細かく調整する必要もあります。
まとめ
MRPと生産スケジューラ(生産計画システム)の概要を説明させて頂きました。
生産スケジューラ(生産計画システム)の最大メリットは「有限能力割付」により【実際に製造できる計画が立案される】事になります。
こちらを実現させるための[設備単位の稼働時間]を登録し、製造する単位を定義する必要があります。
生産スケジューラ(生産計画システム)のメリットは多く存在しますが、システム特性より苦手な内容も存在しております。基幹システム(ERPなど)とデータ連携させて利用する場合は、それぞれの特性を検討して“どのシステムで何を実施させるか”を決めていく必要があります。
例:各品番の必要量計算は基幹システムのMRPで実行し、MRP結果を生産スケジューラ(生産計画システム)へ連携して細かい計画を立案する。
筆者
プロフィール
筆名:スケジューラマイスター
経歴:
トーテックアメニティ株式会社に入社後、生産管理システム導入をプロジェクトリーダとして行ってきた。
その経験を活かしつつスケジューラも担当し、プロジェクトリーダやアドバイザーとして生産スケジューラ(生産計画システム)導入だけで20サイト以上の実務経験を持つ。
また、アスプローバ株式会社が認定する「シニアAPT認定」を保有。
最近は「釣りを趣味にしている」と語っているが、こちらの腕前はよろしくない。
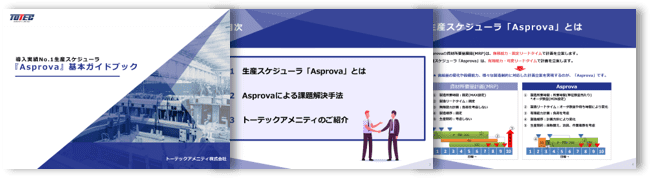
生産スケジューラ『Asprova』
基本ガイドブック
お困りごとがありましたら、お気軽にお問合せください。