プロセス型製造における生産スケジューラ(生産計画システム)導入の難易度について「タンク繰り」
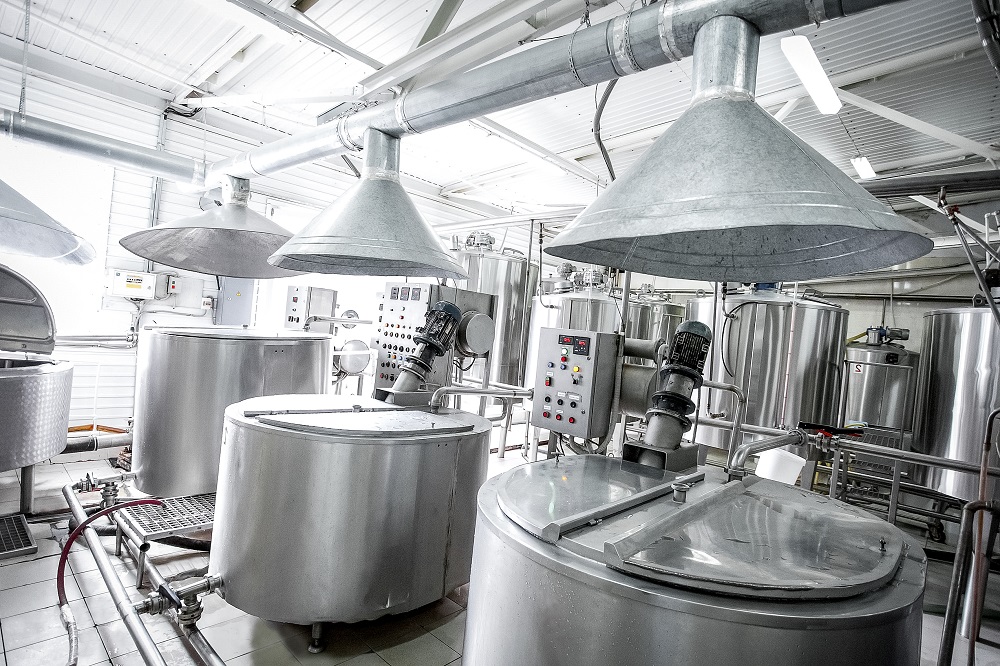
連載テーマ「プロセス製造業でも生産スケジューラが活躍しています!」
- Vol.1 プロセス系製造業における生産スケジューラ(生産計画システム)の計画ロジックとは
- Vol.2 プロセス型製造における生産スケジューラ(生産計画システム)導入の難易度について「タンク繰り」
- Vol.3 プロセス型製造における生産スケジューラ(生産計画システム)導入の難易度について「バッチサイズ・荷姿」
目次
プロセス型製造における生産計画とは
プロセス型製造では、『複雑な制約条件』を加味しながら、効率的かつ実行可能な生産計画を立案する必要があります。
その『複雑な制約条件』の一つに代表されるものとしてタンク繰りが挙げられます。
生産計画に役立つ生産スケジューラ(生産計画システム)に関する資料をダウンロードできます
タンク繰りが難しい理由とは
加工・組立型製造とプロセス型製造の違いの1つとして、半製品の管理方法が挙げられます。
加工・組立型製造では、半製品を平地や棚など制限のない場所に保管できる一方、プロセス型製造では、半製品が液体やペレットであるため、タンクやドラム、コンテナなどに保管する必要があります。
また、液体の半製品は、保管中の品質劣化が懸念されます。
このような特性は、生産計画に大きく影響します。
例えば、下記のような条件を考慮しながら生産計画を立案しなければいけません。
- タンクの数や容量を超えない様に半製品を次工程へ送る必要がある(タンクが製造工程のネックになる)
- タンクに保管する半製品を替える際、洗浄作業が発生するため、同じタンクに同じ半製品を連続で入れる方が効率がよい
- 長期保管すると品質が落ちるため、タンクに保管する期間を○日以内にする必要がある
- タンクごとに、半製品を供給できる後工程ラインが決まっている
- 1つのタンクから複数の設備に繋ぐことが出来る
生産スケジューラ(生産計画システム)導入の難易度とは
近年、複雑な生産計画も高速で立案できる生産スケジューラが注目されています。
しかしながら、計画を立てる際に複数の制約を同時に考えることは、手動であってもシステムであっても容易ではありません。
多くの制約事項が発生するタンク繰り計画は難易度が高く、一般的には加工・組立型製造よりもプロセス型製造の方が、生産スケジューラ導入が難しいと言われています。
今回は、プロセス型製造において、生産スケジューラを利用する際の対応例をご紹介します。
対応例1:生産スケジューラの標準機能を組み合わせた対応
生産スケジューラには、タンク繰りに対応するために有効な機能があります。
資源ロック
後の工程が始まるまでの間、資源(設備)を占有します。
充填タイミングを手動で調整した場合も、占有時間が追従します。 (手動で調整した場合)
重なりMIN、重なりMAX
工程間の時間の上限、下限を設定することができます。
資源有効条件
オーダ、品目、前工程等の情報で、タンク等の設備に計画できる条件を設定することができます。
作業分割
1回のタンクから複数回に分けて充填設備に液を流すなど、1回分の作業を分けて計画することができます。
標準機能の組合せで自動計画を実現できることもありますが、中には実現できない要件もあります。
ここからは、標準機能では自動計画を立案するのが難しい場合の対応例をご紹介します。
対応例2:プラグインでの自動計画の実現
生産スケジューラの標準機能だけでは自動計画を実現できなくても、プラグイン(拡張開発)にて実現できる場合があります。
例えば、配合→タンク→充填のような工順で、配合する設備によって1バッチあたりの配合量が変わる場合を考えてみます。
タンクがネックとなる状態で、バッチサイズを変えながら最適な設備とタンクの組合せを探すのは至難の業です。
以下は、プラグインで計画方法をカスタマイズした事例です。
仮計画を数回行い、その結果から最も良い組合せを採用します。
- 設備を1つ選び、設備に合ったバッチ数を計算する
- 計算したバッチ数で配合→タンク→充填まで計画する
- 全バッチの充填が完了する日時を退避しておく
- 次の設備を選び1~3を繰り返す
- 充填完了日が最も早い設備で計画する
配合設備が3つの場合、以下のような流れです。
・配合設備Aで充填までの仮の計画を立てる
・配合設備Bで充填までの仮の計画を立てる
・配合設備Cで充填までの仮の計画を立てる
・充填完了日時が最も早い、配合設備Bの計画を採用する
ブラグインによる計画は、自由度が高いため様々な要求を満たすことが出来ます。 その反面、計画ロジックが複雑化しすぎて、様々な考慮漏れに後から気づき、なかなか運用に至らないこともあります。 例外ケースを含めた計画要件を十分に洗出して仕様を検討することが重要です。
対応例3:手動調整機能の拡充
自動計画に頼り過ぎず、手動調整機能を拡充させることで、生産スケジューラ導入の目的である「効率化」や「標準化」を達成させる考え方もあります。 下図は、配合とタンクのバッチ数やバッチサイズを調整する画面です。 生産スケジューラが自動である程度計画を立てたあと、 計画担当者が個別に計画を編集します。
登録ボタン押下後に即時でガントチャートに反映されます。 下記のようなルール化が難しい内容に対して、手動調整の効率を上げることができます。
- 需要量に対して余剰が発生するように製造計画を立てる
- 受注量が少ない場合、あえてバッチを細分化し、小さい設備で配合する
- タンクの状態に応じて、タンク使用順を変更する
今回の事例は、プラグイン開発によって実現していますが、標準機能でも手動調整の効率を上げるための仕組みは多数あります。
自動計画がどの程度必要か? ルール化できない要件がないか? ルール化してもマスタのメンテナンスが現実的か? 工場の仕組みや生産スケジューラ導入の目的によって、手動調整機能の拡充を優先的に行うのも1つの手段です。
対応例4:スケジューリング結果から最適解を求める
対応例2と同じように、複雑な要件でも自動計画の精度アップを目指しますが、全く異なるアプローチもあります。
計画ロジックをシステム化せずに、膨大な数のスケジューリング結果から、最適解を提示するSolverという仕組みを使う手法です。
「納期遅れが少ない」、「製造効率が良い」などスケジューリング結果に対する評価ポイントを事前に設定しておくことで、最適な計画パターンを提示します。
Solverの詳細はこちらをご覧ください。
まとめ
いかがでしたでしょうか。 今回はタンク繰りに着目し、プロセス型製造において生産スケジューラの導入が難しい理由と対応例をご紹介しました。
一般的にプロセス型製造業には生産スケジューラが向かないと言われていますが、 上記のように様々な対応方法があります。
工場の仕組みと生産スケジューラ導入の目的に合った対応方法を、柔軟な考えで検討することが、生産スケジューラ導入成功へのカギであると私は考えます。
弊社では、みなさまの生産計画業務における課題解決に向けて、システム構築によるご支援をしております。
生産計画業務効率化に向けたシステム検討の際は、是非ご相談下さい。
筆者
プロフィール
十田 宗匡 Hiromasa Juta
経歴:
入社後2年間、製薬業向け営業支援システムの導入・運用保守を経験。
その後、生産スケジューラ導入に携わり約6年。
現在は関西圏を中心にプロジェクトリーダとして活躍する。
プロセス型製造業への導入支援を得意とする。
アスプローバ株式会社が認定する「シニアAPT認定」を保有。
趣味はお笑いと野球であるが、決して関西色の濃い人物ではない。
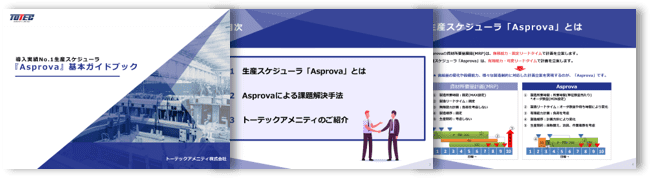
生産スケジューラ『Asprova』
基本ガイドブック
お困りごとがありましたら、お気軽にお問合せください。