プロセス系製造業における生産スケジューラ(生産計画システム)の計画ロジックとは
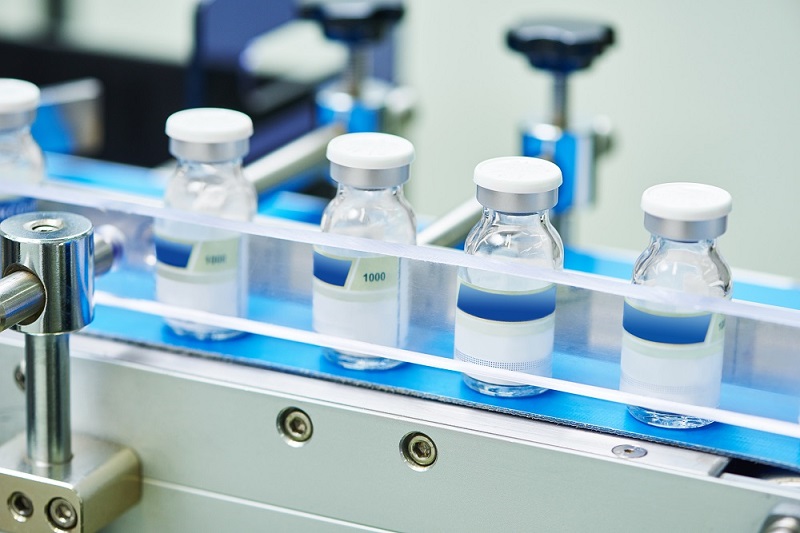
連載テーマ「プロセス製造業でも生産スケジューラが活躍しています!」
- Vol.1 プロセス系製造業における生産スケジューラ(生産計画システム)の計画ロジックとは
- Vol.2 プロセス型製造における生産スケジューラ(生産計画システム)導入の難易度について「タンク繰り」
- Vol.3 プロセス型製造における生産スケジューラ(生産計画システム)導入の難易度について「バッチサイズ・荷姿」
ものづくりを生業とする製造業では、生産を滞りなく進めるために、精度の高い計画を立てなければいけません。
ベテランの計画担当者がExcelや紙を使い時間をかけて生産計画を立てている企業様も多くいらっしゃいます。 しかし、『特急オーダーの発生』や『注文のキャンセル』による生産量の変化、『設備故障』等の予期せぬトラブル が発生する度に、また何時間もかけてリスケジュールする必要があります。 そこで、ベテランの計画担当者のノウハウを落とし込み、最適な計画を高速に立案できる生産スケジューラが 注目されています。
本ブログでは、弊社が様々な製造業に導入した生産スケジューラAsprovaについてご紹介していきます。 業種により、生産スケジューラ適用の難易度も変わってきますが、今回ご紹介させて頂くのは、医薬品(錠剤) を製造しているお客様へ導入した生産スケジューラAsprovaの適用例となります。
プロセス系製造業のひとつである、医薬品(錠剤)製造では、以下のような制約条件を考慮して効率的な生産計画を 立案しなければいけません。
・錠剤毎の大きさや異なる包装方法を考慮した包装計画
・錠剤の連続生産時における清掃時間
このようなスケジューラへの適用が難しい制約条件が存在する場合にも、弊社ではお客様の要望を実現する プラグイン開発を行い、多数の生産スケジューラAsprovaを導入させて頂いた実績がございます。
※今回記載する機能はAsprova標準機能ではなく、プラグイン開発が必要となります。 プラグインについてはこちらで解説しております。
1.生産スケジューラによるロット組み
1.1 背景
用語の説明として、品目種別はバルクと製品の2種類あります。
バルクとは「実際服用する錠剤1粒」を指します。
製品とは、「錠剤をビンやシートなどの入れ物に入った形態」を指します。
今回紹介する事例では、生産は見込み生産です。
下図のように月単位に生産する製品数の情報があります。
製品 | 生産月 | 生産数 |
A-1 | 2022/5 | 200 |
A-2 | 2022/5 | 30 |
A-3 | 2022/5 | 510 |
A-4 | 2022/5 | 0 |
A-1 | 2022/6 | 340 |
A-2 | 2022/6 | 20 |
A-3 | 2022/6 | 210 |
A-4 | 2022/6 | 160 |
製品数から各製品のバルクロット必要数を計算しています。
下図の例では5月はバルクが2ロット必要、6月はバルクが3ロット必要となります。
製品 | 生産月 | 生産数 | バルクロット必要数 |
A-1 | 2022/5 | 200 | 1 |
A-2 | 2022/5 | 30 | 0.3 |
A-3 | 2022/5 | 510 | 1.7 |
A-4 | 2022/5 | 0 | 0 |
A-1 | 2022/6 | 340 | 1.7 |
A-2 | 2022/6 | 20 | 0.2 |
A-3 | 2022/6 | 210 | 0.7 |
A-4 | 2022/6 | 160 | 0.4 |
本機能は、バルク1ロットからどの製品を生産するかの組合せを決定する機能となります。
1.2 機能
本機能では、前述の製品-月単位の生産数をAsprovaへデータ連携し、ロットの組みを行います
ロット組みのルールとして、以下内容で実現しました
ルール1)バルク1ロット=1製品となるような組合せ
ルール2)バルク1ロット=複数製品になる場合、できるだけバルク1ロット内の製品数が少なくなるように組合せ
ルール2-1)ロット組みの基点となる製品を決定します。
優先度1)元のバルク必要数が1ロット以上の製品
※1製品のロット数を減らしたいため
優先度2)生産数の多い製品
ルール2-2)ルール2-1で選択したロット組み基点の製品と合わせてちょうど1ロットになる
製品を一緒に組合せ
※未存在の場合、最も生産数の多い製品を選択し、組合せ
例として、下図の製品をロット組みします。
製品 | 生産月 | 生産数 | 生産数(バルクロット換算) |
A-1 | 2022/5 | 200 | 1 |
A-2 | 2022/5 | 30 | 0.3 |
A-3 | 2022/5 | 510 | 1.7 |
A-4 | 2022/5 | 0 | 0 |
A-1 | 2022/6 | 340 | 1.7 |
A-2 | 2022/6 | 20 | 0.2 |
A-3 | 2022/6 | 210 | 0.7 |
A-4 | 2022/6 | 160 | 0.4 |
5月分のロット組みを行います。
・ルール1により、バルク1ロット=1製品となる組合せを優先します。(製品A-1,A-3)
→製品A-3は残り0.7ロット分となります。
・製品A-2(0.3ロット)とA-3(0.7ロット)でバルク1ロットになるため、
1ロットから製品A-2,A-3を生産するように組合せします
最終的に5月生産のロット組みは以下となります。
生産月 | 組分け | 製品 | 生産数 |
2022/5 | X001 | A-1 | 200 |
2022/5 | X002 | A-3 | 300 |
2022/5 | X003 | A-2 | 30 |
2022/5 | A-3 | 210 |
6月分のロット組みを行います。
・ルール1により、バルク1ロット=1製品となる組合せを優先します(製品:A-1)
→ 製品A-1は残り0.7ロット分となります。
・ルール2により、バルク1ロット=複数製品の組合せを検討します。
・ルール2-1により、ロット組みの基準となる製品を決定します。
・製品A-1の生産量がバルク1ロット以上のため、製品A-1を基準とします。
・ルール2-2により、製品A-1と一緒に生産する0.3ロット分の製品を決定します。
・0.3ロット分だけ生産する製品は無いため、最も生産量の多い製品A-3を一緒に生産します。
→製品A-3は残り0.4分となります。
・製品A-2(0.2ロット)とA-3(0.4ロット)とA-4(0.4ロット)でバルク1ロットになるため、
1ロットから製品A-2,A-3,A-4を生産するように組合せします
最終的に6月生産のロット組みは以下となります
生産月 | 組分け | 製品 | 生産数 |
2022/6 | Y001 | A-1 | 200 |
2022/6 | Y002 | A-1 | 140 |
2022/6 | A-3 | 90 | |
2022/6 | X003 | A-2 | 20 |
2022/6 | A-3 | 120 | |
2022/6 | A-4 | 160 |
ちなみに、組分け”Y002のロット組み基準をA-3とした場合、製品A-1が3ロットへ分割されるため、望ましい結果とはなりません。
生産月 | 組分け | 製品 | 生産数 |
2022/6 | Y001 | A-1 | 200 |
2022/6 | Y002 | A-3 | 210 |
2022/6 | A-1 | 60 | |
2022/6 | X003 | A-1 | 80 |
2022/6 | A-2 | 20 | |
2022/6 | A-4 | 160 |
最後に本機能前提事項として、以下内容があります。
- 月単位のバルク必要ロット数は整数となります。
※員数の関係でバルク必要ロット数が少数の場合でも、整数へ切上げされます。
例) バルクロットが150個で、製品1個でバルク14個必要な場合
製品の生産数が10個の場合、正味の必要なバルクは140個(製品10個×14個/製品)
必要なバルクロット数は0.93(=140/150)であるが、実際は1ロットで生産します。
2.自動計画
自動計画はバルクと製品で異なるロジックで実現しております。
2.1 バルクの自動計画
バルク計画の全体概要として以下となります。
- 生産月-バルクで連続生産となるように計画します。
- ネック工程があるため、ネック工程よりも前工程はネック工程を基点にバックワードで計画します。
- ネック工程よりも後工程はネック工程を基点にフォワードで計画します。
※上記内容はAsprovaの標準機能で実装しております。
例として、以下のバルクを計画します。
生産月 | バルク | ロット数 |
2022/5 | A | 2 |
2022/5 | B | 3 |
2022/5 | C | 2 |
2022/6 | A | 5 |
2022/6 | B | 2 |
2022/6 | C | 3 |
まず、生産月-バルク単位にフォワードで計画します。

工程2がネック工程の場合、工程1と工程2の間が空いてしまうため、工程2を基点に品目単位に工程1を再計画します。
※工程1は品目単位に連続生産したいため、先頭のロットに寄せております。

割付時の主な制約として、プラグインにて、連続生産時の清掃時間考慮や製造時間短縮を対応しています。
例)連続生産時の清掃時間考慮:2ロット単位に清掃時間を考慮

例)連続生産時の製造時間短縮:4ロット目以降は製造時間を短縮する

2.2 製品の自動計画
製品計画の全体概要として以下となります。
- 対象は包装工程の1工程のみです。
- 包装工程は以下要因により、段取りが発生します。 ・包装する錠剤の大きさが異なる
- ・包装方法が異なる
- ・包装するバルクが異なる
- →今回の自動計画では、上記要因で発生する段取り回数が少なくように計画しています。
- ※包装工程の計画はプラグインにて対応しております。
計画方法としては、直近計画した作業に対して、以下の優先度で計画します。
優先度1)同じバルクで組分けされている(前章のロット組みで同じ組分けとなった製品)
優先度2)同じバルクの製品
優先度3)同じ錠剤の大きさを使用する製品
優先度4)包装方法が同じ製品
※優先度2-4については、段取り時間が長くなる要素の優先度を上げております
※優先度2-4について、複数製品が該当する場合、ロット組みされていない製品を優先
例として、以下の製品を計画します。
包装作業 | バルク | 組分け | 錠剤の大きさ | 包装方法 |
1 | A | X001 | 大 | 10個詰め |
2 | A | X001 | 大 | 20個詰め |
3 | A | X002 | 大 | 20個詰め |
4 | B | X003 | 中 | 20個詰め |
5 | B | X004 | 中 | 10個詰め |
6 | B | X004 | 中 | 20個詰め |
7 | C | X005 | 大 | 20個詰め |
最初に包装作業1が計画されたとします。
優先度1(同じロット組み製品優先)により、同じ組分けである包装作業2を包装作業1の後に計画します。
次に優先度2(同じバルク優先)により、包装作業3を計画します。
バルクAの包装作業が存在しないため、次に割付する候補として、バルクBとバルクCがあります。優先度3(同じ錠剤の大きさ優先)により、バルクCの包装作業7を計画します。
バルクCの包装作業が存在しないため、残りのバルクBの作業を計画します。
優先度4(包装方法が同じ優先)により、包装作業4または包装作業6が候補となります。
しかし、包装作業6が包装作業5と同じロットから生産されるため、包装作業6と5は連続して生産する必要があります。 包装作業6を先に計画すると、「(包装作業6)→(包装方法段取り)→(包装方法5)→(包装方法段取り) →(包装方法4)」となり、包装作業5-包装作業4の間でも段取りが必要となります。 そのため、段取り回数を少なくなる包装作業4から計画します。
最終的に以下の計画となります。
3.ロット附番
ロット附番はバルクと製品で異なるロジックで実現しております。
3.1 バルクのロット附番
バルクロット附番方法について、以下概要となります。
- 先頭工程が早く計画されている順番に品目単位にロット番号を付与します。
- 品目単位にロット番号が異なります。(自社製品/他社製品でロット附番ルールが異なります)
- ※アルファベットについて、アルファベットの”I(アイ)”、”O(オー)”は数字の誤認される可能性があるため、使用しない。
- 例)他社製品(A社)の場合、”X-”+連番3桁(X-001→X-002→…→X-999→X-001→X-002)
- ※連番使い切りの場合、0から再附番する
3.2 製品のロット附番
製品ロット附番方法について、以下概要となります。
・ 生産に使用するバルクのロット番号を引継ぎします。
※生産に使用するバルクは生産順番で使用します。
・同じバルクロットから生産する製品は同じロット番号となります
前章での計画結果をロット附番した際は以下となります。
まとめ
今回は、医薬品(錠剤)製造へ導入した生産スケジューラAsprovaの適用例を紹介しました。
生産スケジューラAsprovaではこれらの複雑な計画ロジックに対応し、生産計画業務の効率化や属人化の脱却を実現しました。
また、生産スケジューラAsprovaの導入を適用される際には、実績のある経験豊富な導入支援パートナーの
支援が推奨されます。※導入支援パートナー選定時のポイントはこちらでご紹介
弊社では、みなさまの生産計画業務における課題解決に向けて、システム構築によるご支援をしております。
生産計画業務効率化に向けたシステム検討の際は、是非ご相談下さい。
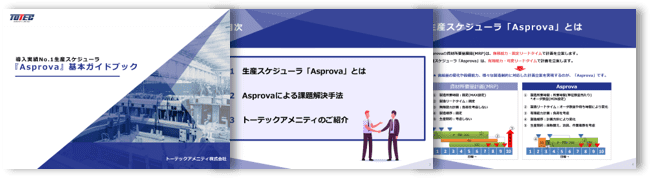
生産スケジューラ『Asprova』
基本ガイドブック
お困りごとがありましたら、お気軽にお問合せください。