導入事例「株式会社飯塚鉄工所様」
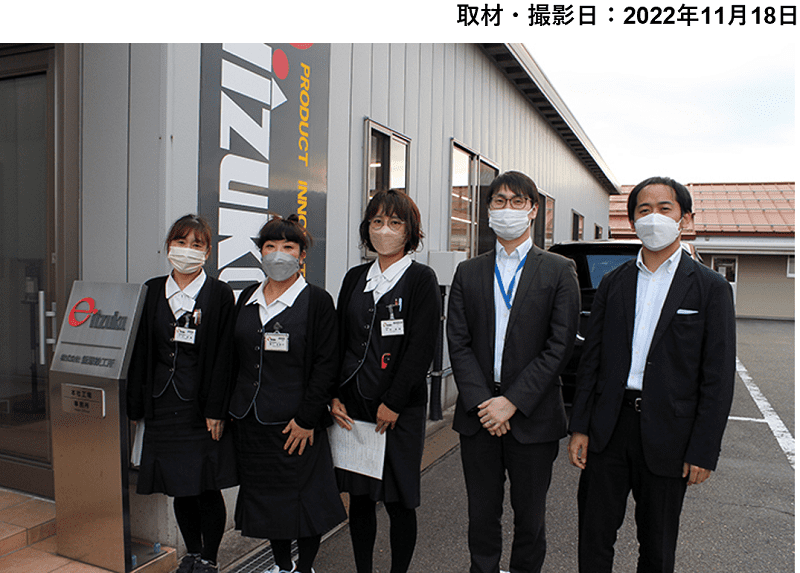
新システムで工場固有のオペレーションを統一
会社の「今」をリアルタイムで見える化し、飯塚ブランドの確立を目指す
流体機器部品製造で高い技術力を持つ株式会社飯塚鉄工所(以下、飯塚鉄工所)では、新システム導入をきっかけとして工場ごとに行っていた独自のオペレーションを統一し、原材料から完成品までの工程が今、どうなっているのかをリアルタイムで把握し、社員全員が同じ情報を共有して経営状況を判断できるようにしました。
TPiCS-XとPI-naviにより生産管理システムを構築し、MotionBoardで見える化することで、資材発注、工程管理、在庫管理などの業務を効率化することに成功しました。
新システム導入の背景には、単に加工するだけでなく、問題解決のできる技術志向の会社を目指す強い意志がうかがえます。新システム導入の経緯と効果について、飯塚鉄工所とトーテックアメニティ株式会社(以下、トーテック)の以下の方々にお話を伺いました。
<飯塚鉄工所>
・代表取締役 飯塚肇氏
・総務部 中町亜希氏(導入プロジェクトリーダー)
・本社工場 資材生産管理部 第1グループ リーダー 小山恵理氏(導入プロジェクトメンバー)
・軽井川工場 資材生産管理部 第2グループ リーダー 鴨下加奈子氏(導入プロジェクトメンバー)
・本社工場 資材生産管理部 部長 中町健氏(導入プロジェクトメンバー)
・軽井川工場 製造部 部長 中村勝宏氏(導入プロジェクト責任者)
<トーテック>
・産業システム事業部 第1システム部 鳥居浩樹(導入プロジェクトリーダー)
・産業システム事業部 首都圏営業部 石井貴也(導入プロジェクトメンバー)
(順不同)
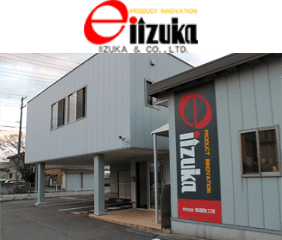
株式会社飯塚鉄工所
住所:新潟県柏崎市半田3丁目15-16(本社工場)
設立:1953年11月
資本金:2,500万円
従業員数:132名(2022年11月現在)
事業内容:流体機器部品(バルブ、ポンプ)、真空機器、医療機器部品、特殊機械部品
株式会社飯塚鉄工所のサイトはこちら
飯塚鉄工所では、材料調達・加工・組立・検査の一貫生産体制で、高精度の流体機器部品や真空機器部品を製造しています。
飯塚鉄工所について
初めに飯塚鉄工所について伺いました。
代表取締役 飯塚氏
飯塚鉄工所は、石油精製工場で使われるポンプやバルブなどの流体部品の修理工場として1953年に創業しました。
かつては柏崎市で石油が出ましたので、石油ポンプの需要が大きかったのです。しかし、石油産業が下火になったため、「修理から作る」を目標に複合加工機を導入し、LNGポンプ、真空ポンプ、精密バルブなどの流体部品の製造に挑戦しました。
創業当初は12名ほどの工場でしたが、今では5拠点で約132名の従業員が働くまでに飛躍しました。
きっかけは、人工透析などの医療機器の部品を手がけたことです。
弊社では、材料調達、加工、熱処理、表面加工などを一貫して手がけることができるので、高い品質要求に応えられます。
飯塚鉄工所のサプライチェーン
単に設計図どおりの製品を作るのではなく、これまで培ってきたノウハウと技術力を使って、軽くする、安くする、早く作るなどの提案をできることが弊社の強みです。
「熱意、挑戦、奉仕」を社訓として発展してきた弊社ですが、現在は、技術提案、品質、納期遵守、社員、競争力の面でお客様から信頼いただける「飯塚ブランド」を確立することを事業テーマとしています。
今後は、飯塚ブランドをさらに発展させ、生活水準、もの作りなどの面で日本の社会へ貢献することを目標にしています。
飯塚鉄工所の技術力・提案力
オペレーションを統一する決断
事業が拡大するにつれ、工場の数が増え、今では4工場、1倉庫、1営業所という規模になりました。
しかし、それぞれの工場で生産管理、資産管理、工程管理などのオペレーションが異なっていました。
実は、これは意図的にそうしていたところがあります。システムを導入して運用を統一化し、効率化するというのはプラスのように聞こえますが、個性を殺してしまうというマイナスを伴います。
そのため、資材発注などが非効率になるのは承知の上で、各拠点の強みと弱みが明確になるまでは異なるオペレーションのままにしておきました。
個性のない工場は、ただの加工屋さんになりかねません。そうではなくて、より良い製品を提案できる強みを持たなければ、小さな会社の活躍できる場がなくなります。
新システムを導入するきっかけは、各拠点の強みと弱みが把握できたタイミングで、従来使っていたシステムが陳腐化してしまい、サーバーもリプレースするタイミングが来たことです。
同時に従来の工場長制度を改め、事業部制に移行しました。つまり、新システム導入と組織改革の2つを同時に行う決断をしました。
かつては、拠点ごとに異なるオペレーションだった
トーテックをパートナーに
弊社のお客様が新しいシステムを導入された際に、弊社にはその影響が全くなかったことがありました。そのお客様に聞いてみると、システム導入を担当したのはトーテックさんだということでした。
そこからトーテックさんと弊社の間で新システム導入のお話が始まります。単にパッケージソフトを組み合わせるだけではなく、高い技術で機能を作り込んで要望に応える。
ソフトメーカーには真似のできない、そんなビジネススタイルが魅力でトーテックさんを気に入り、システム導入のパートナーに決定しました。
新システム導入へ
工場ごとに異なっていた運用を統一し、新システムに移行するという、むずかしいチャレンジをどのように実現したのかを伺いました。
新システム導入プロジェクトリーダー 中町氏
社長の決断を受けて、新システム導入プロジェクトを作り、まず社長がプロジェクト責任者として就任しました。私はプロジェクトリーダーで、メンバー3名は全員女性です。
「鉄工所」というと、どうしても男っぽいイメージがあるので、女性に活躍して欲しいという社長の思いにより任命されました。総務部に所属しているので、現場から一歩引いた目線で見られたことが良い結果に結びついたと思います。
システム導入のプロジェクトリーダーは初めてでしたし、当初は工場ごとのオペレーションや考え方の違いが大きく、どうなることかと思いました。
当然、現場からの反発も予想されましたが、プロジェクト責任者である社長から「現状を維持するのではなく、向上させていくために新システムを導入する」という強いメッセージが出されていたので、各工場の代表が集まって、それぞれのオペレーションについて理解するところから始めました。
要件定義の打ち合わせを重ねていくと、同じ業務でも工場が違うと「そんなやり方をしているのか」という発見が数多くあり、相互理解にもつながりましたし、オペレーションを統一すべきだという機運が生まれました。
トーテックさんとは週1回ペースで要件定義の打ち合わせを行っていましたが、コロナ感染が拡大したタイミングで打ち合わせが途切れてしまい、かなり時間をロスしてしまったのが悔やまれます。
その後、オンラインで打ち合わせを再会し、社内の議論が行き詰まったときなどには、他社事例やアドバイスなどを提供していただきながら要件定義を進めました。
さまざまなディスカッションを重ねた結果、新システムはTPiCS-XとPI-naviを組み合わせた生産管理システムとMotionBoardを使った見える化の機能で構成し、以下のような目標を持ってスタートしました。
- オペレーション統一によるシステムの統合化
- 在庫・仕掛在庫の把握(資産管理)
- グローバル対応(外貨)
- 生産状況・進捗の見える化
- 次世代に向けた拡張性のあるシステム
トーテックから提案した新システム全体像
オペレーションの統一と見える化を実現
工場ごとの違いを乗り越えて、導入した新システムの効果について伺いました。
新システム導入プロジェクトメンバー 鴨下氏
以前に比べると、あちこちに散らばっていた情報が1つにまとまったのが大きなメリットです。
例えば、工程の中で、今、何がどうなっているのかがリアルタイムで見えるようになりました。
以前は、材料、仕掛かり、在庫が別々の画面で表示されていたので、この後どのくらい発注すればいいのか、在庫はどのくらいになるのかが把握しにくかったのですが、今は1つの画面で見られるので、現状がどうなっていて、今後どうなるのかが一目瞭然です。
新システム導入プロジェクトメンバー 小山氏
プロジェクトを立ち上げた頃は工場ごとのオペレーションや考え方の違いばかりが目立ちましたが、お互いのやり方を理解し、ディスカッションする中で溝が埋まっていき、新システム導入に向かって一丸となって進むことができました。
システム導入のプロジェクトに参加するのは初めてだったので責任の大きさを感じていましたが、会社の変化に立ち会えたことが良い経験になりました。
現場では
製造現場では新システムをどのように活用しているのかを伺いました。
右:軽井川工場 製造部 中村氏
左:本社工場資材生産管理部 中町氏
製造の進捗がリアルタイムで共有できるので、不良が出た場合にどの工程でどのくらい発生したかがすぐに把握できます。早く対策を取れますし、ボトルネックになっている工程も一目でわかります。
進捗入力用のタブレットをすべての工作機械に装備したので進捗状況がリアルタイムで把握できますし、検査の情報もタブレットで入力しています。
入力した情報をMotionBoardで見える化し、各工場の操業状態が共有できるようになりました。
MotionBoardを使って情報を見える化している
タブレットで工程の進捗を入力する
タブレットで検査情報を入力する
TPiCS-XとPI-naviを組み合わせた生産管理システムで受注から出荷までの処理を行う
今後に向けて
最後に、システムの今後について伺いました。
新システム導入プロジェクトリーダー 中町氏
オペレーションの統一と新システム導入ができたので、新システム導入プロジェクトの目標はクリアできました。
同じ情報をリアルタイムで共有するだけでもかなりの改善ですが、今後はさらに進めて、共有した情報を活用する方法の検討が課題です。
システムの今後についても、MRP(Material Requirements Planning:資材所要計画)などTPiCS-Xの強みを生かして発展させることを考えています。
業務の自動化を進めて、属人化させずに誰でも運用できるようにしたいですし、人的作業そのものを減らしたいと思っています。
トーテックとのパートナーシップ
以前のシステムでは業務をシステムに合わせなければなりませんでしたが、新システムでは業務にシステムを合わせるべきだと感じていました。
弊社の要望を実現するにはパッケージソフトのカスタマイズでは無理で、「飯塚鉄工所のシステム」として構築できるパートナーが不可欠でした。
今回は、弊社の要望にトーテックさんの提案がうまくマッチし、提案内容を高い技術力で実現していただきました。
今後もトーテックさんと一緒に進めていきたいと思っています。
トーテック担当者のコメント
新システム導入のプロジェクトリーダー鳥居
工場ごとに独自のやり方だったオペレーションを統一するのが今回のプロジェクトの目標でした。そこは達成できたと思います。
2021年7月に新システムに切り替えて最初の1か月は多少の混乱はありましたが、私が柏崎市に長期滞在し、すぐに対応できる体制を整えていたので1か月程度で修正できました。
現在は、社員の方がシステムに慣れてきましたので、さらに使いやすくするためのご要望にお応えしています。
飯塚鉄工所の方もおっしゃっていましたが、パッケージソフトの組み合わせでは実現できないことがありますので、ご要望に合わせてシステムを作り込んでいくことが大事です。
プロジェクトメンバー、工場代表メンバーとディスカッションしながら、作り上げたことが成功の要因だと思います。
取材メンバーの皆様とトーテック担当メンバー
飯塚鉄工所の微細な加工技術により、新たなものづくりとしてチャレンジした商品、JAPAN DON~じゃぱんどん~
取材日:2022年11月18日
記載の担当部署は、取材時の組織名です。
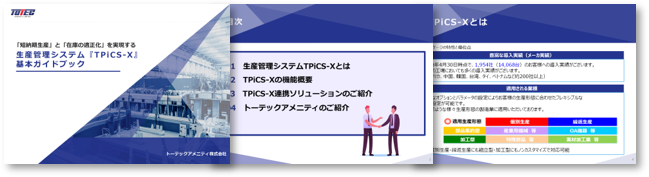
生産管理システム『TPiCS-X』
基本ガイドブック
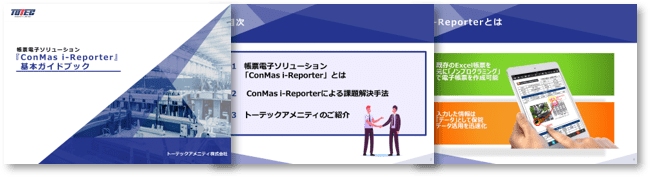
電子帳票ツール
『i-Reporter』
基本ガイドブック
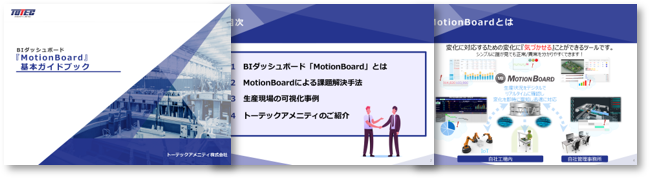
BIダッシュボード『MotionBoard』
基本ガイドブック
お困りごとがありましたら、お気軽にお問合せください。