導入事例「本田技研工業株式会社様」
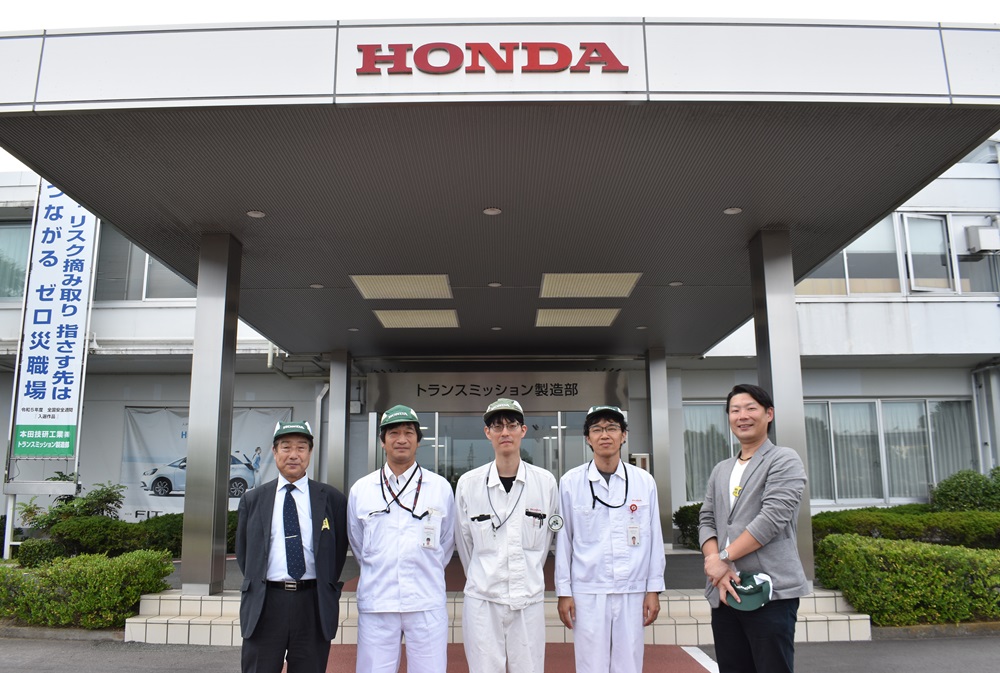
MotionBoardにより製造ラインの稼働状況をリアルタイムに把握
i-Reporterにより帳票作成を自動化し、作成時間を1/8に
技術支援を受けながら、自分たちでツールを作り、進化させていく
1948年に本田技研工業株式会社(以下、ホンダ)が誕生し、「日本一、世界一の二輪車メーカーに」という夢を託し名付けられた、ホンダ初の二輪車「ドリーム号」が生まれました。この黎明期の1954年に現在のトランスミッション製造部が浜松に設立されました。トランスミッション製造部はホンダ発祥の地にあって、その芽生えから今日まで、ものづくりの拠点として歩み続けています。
CVT(無段変速機) e:HEV(2モーターハイブリッドシステム)
―― トランスミッション製造部の主な製品 ――
トランスミッション製造部では製造ラインの稼働状況を把握するのに手間と時間がかかっていたため、稼働状況の見える化に挑戦しました。MotionBoardとi-Reporterを導入し、当初は自分たちでカスタマイズしていましたが、思うような成果が出ません。そのため、MotionBoardとi-Reporterの経験を持つトーテックアメニティ株式会社(以下、トーテック)が技術支援パートナーとして選ばれました。
MotionBoardとi-Reporterを導入し、どのような技術支援を得て、成果を上げたのでしょうか。導入の経緯と今後について、次の方々に伺いました。
<本田技研工業株式会社>(発言順)
浜松工場 管理課 アシスタントチーフエンジニア 足立和也氏
浜松工場 ギア加工モジュール アシスタントチーフエンジニア 加藤俊和氏
浜松工場 アルミ塑加工モジュール 疋田健清氏
浜松工場 アルミ塑加工モジュール アシスタントチーフエンジニア 小杉亙氏
<トーテックアメニティ株式会社>(発言順)
産業システム事業部 第1システム部 第2グループ 主任 佐藤諒明
産業システム事業部 第1システム部 第2グループ 上席リーダー 横井勝敏
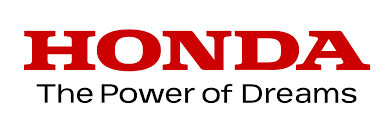
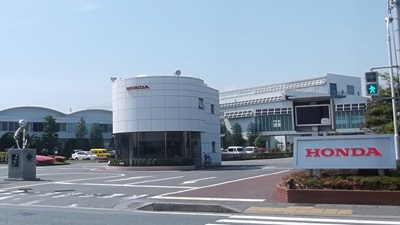
本田技研工業株式会社
本社:東京都港区南青山2-1-1
設立:1948年9月
資本金:860億円(2024年6月現在)
従業員数:連結194,993名、単独32,443名(2024年7月現在)
事業内容:二輪車、四輪車、パワープロダクツの製造販売
本田技研工業株式会社のサイトはこちら
製造ラインの稼働状況をリアルタイムに把握する
浜松工場 管理課 アシスタントチーフエンジニア 足立和也氏
「製造ラインの稼働データを紙に書き写し、Excelに転記して日報を作っていたので、問題対応までに時間がかかっていました」
製造ラインの稼働状況を見える化するきっかけは、製造拠点間で製造ラインの水準を比較するプロジェクトに私の部署が選ばれ、その担当者になったことです。当時は、製造ラインの稼働状況は月次で報告していました。製造ラインを回り、データを紙に書き写し、Excelに転記するというやり方です。報告のタイミングが1か月に1回になりますので、問題の対策までに時間がかかっていました。これをなんとか2~3日で把握することを目標にしてMotionBoardを導入しました。
最初のステップとして、稼働状況のデータを取れるようにしました。次にデータの見える化に挑戦したのですが、これがなかなかうまく行きません。
こういうシステム開発はベンダーさんにお願いすることが一般的だと思いますが、それではシステムを進化させるのが難しい。製造現場は日々進化しているので、自分たちが欲しいと思うツールを自分たちで作り、進化させるべきだと考え、自力開発に取り組みました。
まずはMotionBoardのメーカー研修でいろいろ教わりましたが、データベースへの接続もできないような状態でした。実現したいことはあるのですが、実現する方法がわからず、なかなか前に進みません。そこでトーテックさんにお願いして、わからない部分を教えていただく技術支援をお願いしました。
―― 事務室内から製造ラインの稼働状況をモニターする ――
―― 稼働状況を確認するMotionBoardの実際の画面 ――
やりたいことが明確なので、適切な技術支援が可能に(トーテック 佐藤諒明)
産業システム事業部 佐藤諒明
技術支援の前にホンダ様とどうデータを活用するかについて打ち合わせをしたところ、見える化したいこと、分析したいことが明確になっていることがよくわかりました。何をどう見える化したいのかというホンダ様のイメージに合わせて、弊社から対象データの選定や加工方法をご提案し、レクチャーする「伴走型の技術支援」を進めることとなりました。開発の主役はホンダ様で、弊社が必要なサポートを行います。
当初、ホンダ様はかなり大きなゴールをお考えでしたが、実際の開発ではテーマを絞り、スモールスタートで見える化を実現し、徐々に範囲を広げていったことも成功の要因の一つだと思います。本業と両立させながら、手を広げすぎずにできる範囲から進めていくことで手戻り修正や変更もすばやく反映できます。
データ取得と帳票作成を自動化し、作成時間を1/8に
浜松工場 ギア加工モジュール アシスタントチーフエンジニア 加藤俊和氏
「紙の報告書からの脱却を目指しています」
私は、i-Reporterを使った帳票の電子化、ギア加工モジュールのDX化を担当しています。弊社には報告や情報共有を紙で行う文化がありましたので、紙の帳票はまだまだ量も種類もあります。しかし、その弊害が目立っています。特に問題なのが報告作成にかかる手間と時間です。以前のやり方では、製造ラインを巡回してデータを紙に書き写し、Excelにまとめていたので、日報作成に2時間ほどかかっていましたが、今はi-ReporterとConMas IoTの組み合わせにより30分に短縮できました。
帳票電子化は、第1弾を日報作成の電子化にし、第2弾を製造ラインの稼働データの自動取得に絞りました。i-ReporterとConMas IoTの組み合わせによりデータをワンタッチで取れるようにしたため、報告書の作成時間を1か月40時間から5時間に短縮できました。
現場で成果が出ればいいのですが、せっかくツールを作っても現場で抵抗を受けることもあります。そういうときは現場の上司に働きかけて、使ってもらうようにお願いし、メリットを現場に感じてもらえるようにしています。
浜松工場 アルミ塑加工モジュール 疋田健清氏
「変動要因が多い製造設備の稼働データを自動で取得する取り組みをしています」
以前は「i-Reporterって何?」という空気が現場にありましたが、いったんリアルタイムでデータが入手できるようになると、必要不可欠なものになりました。サーバーをリプレースするのでi-Reporterをいったん止めますと現場に話したときに、i-Reporterがないと仕事に支障が出るので止めないでくれと強く言われたほどです。
しかし、うまく行っている現場ばかりではありません。私の担当しているアルミ鋳造機械モジュールには巨大なアルミ鋳造機が4基ありますが、ここは苦戦しています。鋳造の不具合は、複数の原因が絡み合うので、データだけで判断せず、人の目で見て解決することが多いからです。会社の監査ルールが紙で記録を残すようになっていることもあり、今は紙の報告書がメインですが、いずれは紙をゼロにしたいと思っています。
―― 製造ラインの稼働データを取得する ――
ホンダ様と協力して、高い要求を実現(トーテック 横井勝敏)
産業システム事業部 横井勝敏
i-Reporterを使ってデータ取得の自動化や紙帳票を電子化するだけなら難しくはないのですが、ホンダ様の要求レベルが非常に高く、標準以外の機能を駆使して実現しました。佐藤がお話ししたように自分たちのツールは自分たちで作り、進化させていくという意思をお持ちなので、弊社は技術支援に徹し、実装の主体はホンダ様という役割分担になりました。
ホンダ様には、自力で開発する意思とデータの蓄積、分析手法が揃っているので、技術支援だけで成果を出せましたが、条件の整っていない会社では請負開発の方が向いている場合もあるかと思います
浜松工場 アルミ塑加工モジュール アシスタントチーフエンジニア 小杉亙氏
「よくできたツールであっても現場で使ってもらわなければ意味がありません。そこが工夫のしどころです」
私は、足立と加藤が導入したMotionBoardとi-Reporterを活用してアルミ加工ユニットの効率化に取り組んでいます。まだまだ課題はたくさんありますが、一つ一つ解決して、製造ラインの効率化につなげています。
MotionBoardとi-Reporterの導入から5年ほど経ちましたので、使っている部署はかなり増えてきましたし、浜松工場以外の工場でもMotionBoardを導入する例が増えてきています。データを見える化し、すぐにアクションを取れる点が評価されていると感じます。
しかし、いざ自分の担当する製造ラインに目を向けると、せっかく作ったツールが現場で使ってもらえないことがあります。紙帳票に慣れている、今までのやり方を変えるのが不安だ、と理由はいろいろですが、ツールを使わない人が出てしまいます。しかし、製造現場が現状維持で良いわけがありません。データを活用し、リアルタイムで状況を把握して、どうすればいいかを自分たちで考える。そうなるように仕向けたいと思っています。
―― 製造ラインの進捗状況を共有する ――
目標は、データドリブンなホンダ
浜松工場 管理課 アシスタントチーフエンジニア 足立和也氏
「DX化を推進できる人材を増やし、ホンダの工場全体をデータでつなぎたいですね」
MotionBoardとi-Reporterの組み合わせでデータの見える化、帳票の電子化、作成の自動化は進みつつあります。浜松工場以外の工場でもMotionBoardとi-Reporterの利用は増えています。工場のDX化は進みつつありますが、まだ個別の工程をDX化している段階です。ホンダには工場がたくさんあり、さまざまな工程があります。前後の工程がデータを共有して動けば、さらに効率を上げられるのは間違いありません。
そのためにはDX化を推進できる人材を増やすことが大事です。トーテックさんから技術支援を受けたように、今では私たちが社内の部署にMotionBoardとi-Reporterの技術支援を行っています。その際にも、やりたいことを明確にしてもらい、具体的な実現方法を考えるようにしています。技術支援を続けた結果、浜松工場にある8部門それぞれにSQLが書けてテーブルを作れる人が3~4名誕生しました。
MotionBoardとi-Reporterの導入では成果を出せたので、さらにDX化を推し進め、ホンダの工場全体がデータドリブンで動くようになることを目標にしています。
取材日:2024年6月17日
記載の担当部署は、取材時の組織名です。
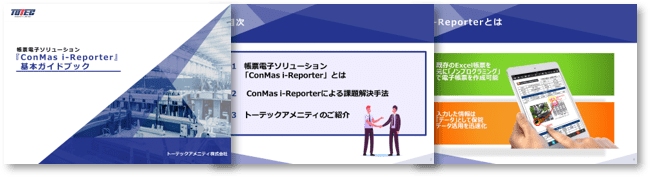
電子帳票ツール「i-Reporter」
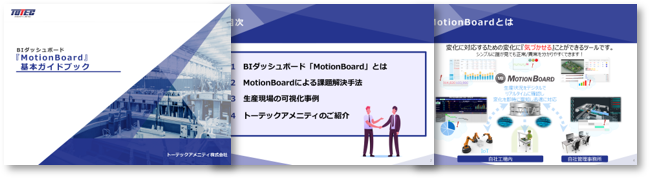
BIダッシュボード「MotionBoard」
お困りごとがありましたら、お気軽にお問合せください。