導入事例「杉松産業株式会社様」
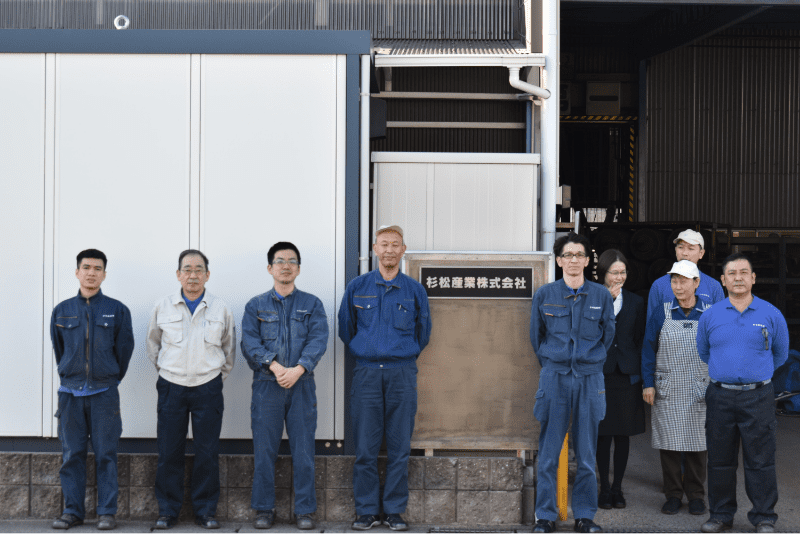
製造設備の稼働データを見える化することで、不良率が1/3に
工場の自働化と災害対策により、事業の継続性を追求
鋳物製造に欠かせない部品である、中子の製造を手がける杉松産業株式会社様(以下、杉松産業)では、紙で記録していた製造設備の稼働データをi-Reporterで入力し、MotionBoardで見える化を実現。
データを社内共有することで生産性の向上、不良率の低減に成功しました。
新システム導入の経緯と効果について、杉松産業の以下の方々にお話を伺いました。
<杉松産業>
・代表取締役社長 杉浦正広氏
・小垣江製造部 主任 小林亮太氏
・製造自働化部 班長 兼 IT関係担当 生川雅貴氏
<トーテックアメニティ>(以下、トーテック)
産業システム事業部 ソリューション営業部 岩田竜也
(順不同)
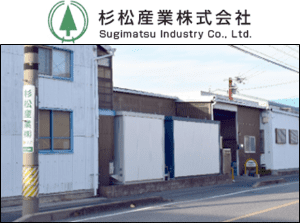
杉松産業株式会社
住所:愛知県刈谷市小垣江町本郷下50番地3
創業:1964年4月
設立:1977年12月
資本金:1,000万円
従業員数:25名
事業内容:鋳造用中子(シェルモールド)の製造
本書に記載の会社名、製品名等は、各社の商標または登録商標です。本書では、商標表示(®、™)は表示していません。
杉松産業について
初めに杉松産業について伺いました。
―― 代表取締役社長 杉浦氏 ――
鋳物製造で使う中子とは、中空構造の鋳物を作る際に鋳型の中に入れて、鋳物の中に空間を作り出すものです。
鋳物は鋳型の中に溶けた金属を流し込んで作りますが、鋳型内に中子を入れると、金属が流れ込まずに製品の中に空間を作れます。
―― 鋳物製造で使われる中子 ――
弊社の中子製造は、戦後、私の両親が鋳物を製造する中で、さまざまな中子を自分たちで作ったことが始まりです。
ドイツで発明されたシェルモールド法という方法で製造しています。
これは樹脂でコーティングされた砂を280~300℃に熱した金型に入れて焼き固め、その後、バリ取り、接着、塗型などを行って、完成させるという方法です。
複雑な形状でも成型しやすいことや、その精度を高くできることから、自動車のエンジン、デフケース、トランスミッションケースなどの製造に多く使われています。
―― シェルモールド中子の成型工程 ――
―― シェルモールド中子の製造現場 ――
中子は鋳物に欠かせない部品ですが、零細企業が多く、従業員を雇う規模で中子を製造している会社は多くありません。
その理由は、職場環境です。先ほど説明したように、シェルモールド法では熱した金型を使いますが、以前は金型の移動、交換、清掃などをすべて人手で行っていました。
高温の金型や中子に素手では触れませんので、軍手を何重にもはめて扱います。
高温の金型の近くで作業しますから、夏は気温が45℃ぐらいまで上がり、仕事をするだけで痩せてしまうような環境でした。かつては仕事が少なく、きつい職場環境でも人が集まりましたが、今となってはいわゆる3K職場と見なされ、人が集まりません。
これではいけないと思い、10年ほど前から職場環境の改善に取り組み始めました。
最初に手を付けたのは、製造品種の絞り込みです。
愛知県は自動車産業が盛んなため、エンジン関連のさまざまな種類の中子を製造していました。
しかし、今後、自動車の電動化が進めばエンジン関連の部品は先細りになるので、電動化された自動車にも必要なブレーキ関連に軸足を移しました。
続いて、手作業に頼ってきた成型作業の自働化を進めました。ロボットアームを導入して、成型機から中子を取り出す作業、取り出した中子のバリを取る作業を自働化しました。
高温の中子に触れることがなくなったため、作業者はつらい作業から解放され、生産性の向上にもつながりました。
製造現場の改善と合わせて、事務作業の効率化にも少しずつ手を付けました。
製造だけではなく、会社全体をバランス良く改善することが大事だと思ったからです。
それまでは、何事も紙と電卓で処理していましたが、Excelで見積もりを出せるようにするところから少しずつ手を付けました。今では、会計システムを導入してさらに効率化を進めています。
製造現場と事務作業の改善に手を付けてみて、何をシステム化すれば、業績が伸ばせるかを見極めることが大事だということを痛感しました。
しかし、素人にはシステム化の効果を見極めるのは簡単ではありません。ここから試行錯誤を始めました。
トーテックとの出会い
システムを導入して、生産性を上げるにはどうしたらいいか?一人で考えていても答えが見つからないので、展示会やセミナーをいくつも回って、情報を集め、パートナーとなる会社を探しました。
そんな中、とあるセミナーで出会ったのがトーテックさんです。
セミナーの説明が求めている内容と合っていたし、親身になって話を聞き、弊社が抱える問題を解決に導く提案を作ってくれました。
当時、導入を検討していたシステムの候補が2つあったのですが、i-Reporterは素人でも扱えると感じたのでトーテックさんをパートナーとして選びました。
i-Reporterで製造現場の省力化
―― 小垣江製造部 主任 小林氏 ――
かつては中子を人手で製造していたため、製造設備の稼働状態、不良の原因解析などを職人のカンやコツで行うことがありました。
しかし、それでは客観的な状態を把握できないので、製造設備にセンサーを取り付け、稼働データをモニタリングできるようにしました。
これにより、不良が発生したら原因解析と対策が素早く行えることを期待していたのですが、すぐにはうまく行きませんでした。
原因の1つとしては、確かにセンサーでデータは取れるのですが、そのデータは各作業者が紙の日報に記録し、終業時に提出していました。
その日報を集めて、別の人がデータを集計して、ようやく製造設備全体のデータが出そろうという状態でした。
これでは、時間もかかるし、人手もかかる。せっかくのデータをもっと活用するためにトーテックさんに相談しました。
トーテックさんからの提案は、紙の日報をタブレット端末に置き換え、作業者が生産管理データ、作業日報をi-Reporter上で入力するというものでした。
―― 以前の稼働データ処理方法 ――
―― i-Reporterを使った稼働データ処理方法 ――
とは言え、紙の日報を急にタブレット端末に置き換えたわけではありません。高齢者や外国人からは反発がありましたし、タブレット端末に不慣れな人もいました。
トーテックさんには、タブレット端末の使い方講習会を開いていただき、紙の日報からタブレット端末に変わっても違和感を抱かない画面設計にしてもらいました。
数ヶ月もすると、現場でも当たり前のようにタブレット端末で入力するようになり、データ処理にかかる人手が減って、データがすぐに見られるようになりました。
―― 製造現場で使われるタブレット端末 ――
MotionBoardで見える化して、不良率を1/3に
―― 製造自働化部 班長 兼 IT関係担当 生川氏 ――
当初はタブレット端末を使うことに現場でのとまどいもありましたが、データ集計が速くなった効果は明確に現れました。
現場の監督者が集まる会議では、データを見ながら工程の改善点が把握できるため、対策の検討が容易になりました。
カンやコツに頼らずに客観的に検討できるようになったので、不良率が3%から1%に減少しました。
また、i-Reporterで集計したデータは、MotionBoardを使って、見える化しています。
―― MotionBoardで見える化した稼働データ ――
トーテックさんとは二人三脚でシステム化を進めている感じです。毎週1回は来ていただけるので相談しやすいですし、手厚くサポートしてもらっています。
今後に向けて
最後に、杉松産業の今後について伺いました。
―― 代表取締役社長 杉浦氏 ――
今後、弊社で目指したいのは、工場の自働化と災害対策です。工場の自働化では、製造現場を自働化し、品質確認をリモートで行って、工場に人がいない状態を目指します。
災害対策としては、現在の工場がある小垣江という土地は海抜が低く、自然災害に弱いので、将来にわたって事業を続けるため工場を安城市に増築したいと思っています。
どちらも簡単なことではなく、時間はかかると思いますが、必ず実現したいと思っています。
今のまま、事業を続けても勝ち目はないだろうと強く感じています。
工場の自働化にはシステム導入は不可欠なので、今後もお互いの得意分野を生かして、トーテックさんと協力を進めていきます。
また、現在の事業の柱は中子製造だけなので、次の事業の柱を立てたいと思います。
そのヒントは、弊社のような小さな会社が今後どうやって生き残っていくかを考えたときに得られるのではないでしょうか。
弊社のような小さな会社が規模の大きな会社に立ち向かっていくには、小さなもの同士が団結して、力を合わせなければなりません。
今の世の中で広く行われているのは「競争」ですが、これが「共創」になり、やがては「協創」になっていくだろうと思います。
小さくとも、力を合わせて共創から協創へ発展させていくため何をすべきか。ここに今後の事業のヒントが隠れています。
トーテック担当者のコメント
製造設備の稼働データをMotionBoardで単純なグラフとして表示するだけではなく、i-Reporterを使って入力した作業実績や不良情報を現場で見える化し、生産性の向上につなげる取り組みは、当時としてはあまり経験のない試みでした。我々も勉強させてもらいながら、杉松産業様と二人三脚で進めたことで、うまく現場にシステムが浸透したと感じます。
今後もご要望を伺いながら、さらに生産性を上げられるように協力させていただきたいと思っています。
取材日:2023年1月17日
記載の担当部署は、取材時の組織名です
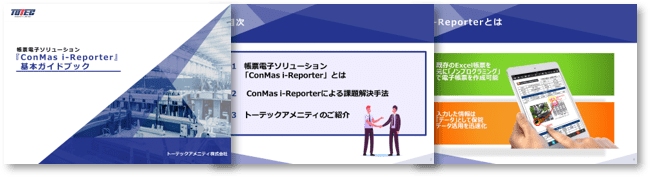
電子帳票ツール
『i-Reporter』
基本ガイドブック
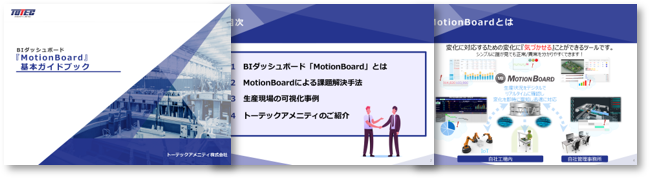
BIダッシュボード『MotionBoard』
基本ガイドブック
お困りごとがありましたら、お気軽にお問合せください。