導入事例「株式会社コーヨーテクノス様」
ブラックボックス化していた生産工程を見える化
TPiCS-XとPI-naviの組み合わせでシステムを業務に最適化
データを活用して生産性を上げ、骨太な会社へ
株式会社コーヨーテクノス(以下、コーヨーテクノス)は、1995年の創業以来、半導体関連の検査用各種プローブカードやプリント基板関連の検査用治具、ICソケットなどの開発・製造・販売を行い、製品の小型化に対応したワイヤープローブではトップクラスの小型サイズを実現しています。
また、EVなどに搭載されるパワー半導体の検査治具でも競争力を発揮しています。半導体、プリント基板の検査治具はお客様の設計に合わせてオーダー品として設計・製造しています。
プローブカード 様々な形状のプローブユニット
―― コーヨーテクノスの主な製品 ――
以前のコーヨーテクノスでは、受注登録以降の生産工程を管理する仕組みが整っておらず、現場の経験と知識を活用して生産していました。
主に電話やホワイトボードを使って進捗状況や生産実績を共有しており、生産状況がデータとして蓄積されていなかったため効率化や生産性向上のための分析が難しくなっていました。
こうした課題を解決し、生産状況をデータで把握して生産性を向上するため、新生産管理システムの導入を決定しました。
約30社の生産管理システムを比較検討し、導入パートナーとして選ばれたのがトーテックアメニティ株式会社(以下、トーテック)です。
トーテックは、新生産管理システムを構築するために攻撃型生産管理システムTPiCS-X(以下、TPiCS-X)とイージーオーダー型テンプレートPI-navi(以下、PI-navi)を組み合わせたシステムを提案し、コーヨーテクノスと協力して開発・導入しました。
TPiCS-XとPI-naviを組み合わせた新生産管理システムをどのように開発し、導入したのでしょうか。開発・導入の経緯と今後について、次の方々に伺いました。
<株式会社コーヨーテクノス>(発言順)
事業戦略推進部 取締役部長 長尾積憲氏
総務部 常務取締役総務部長兼経理部長 土橋賢太郎氏
営業技術部 係長 小林大樹氏
製造部 生産管理課 係長 山岸康弘氏
製造部 生産管理課 御子柴聡一氏
製造部 製造1課 課長 伊藤尚武氏
<トーテックアメニティ株式会社>
産業システム事業部 第1システム部 第1グループ 鳥居浩樹

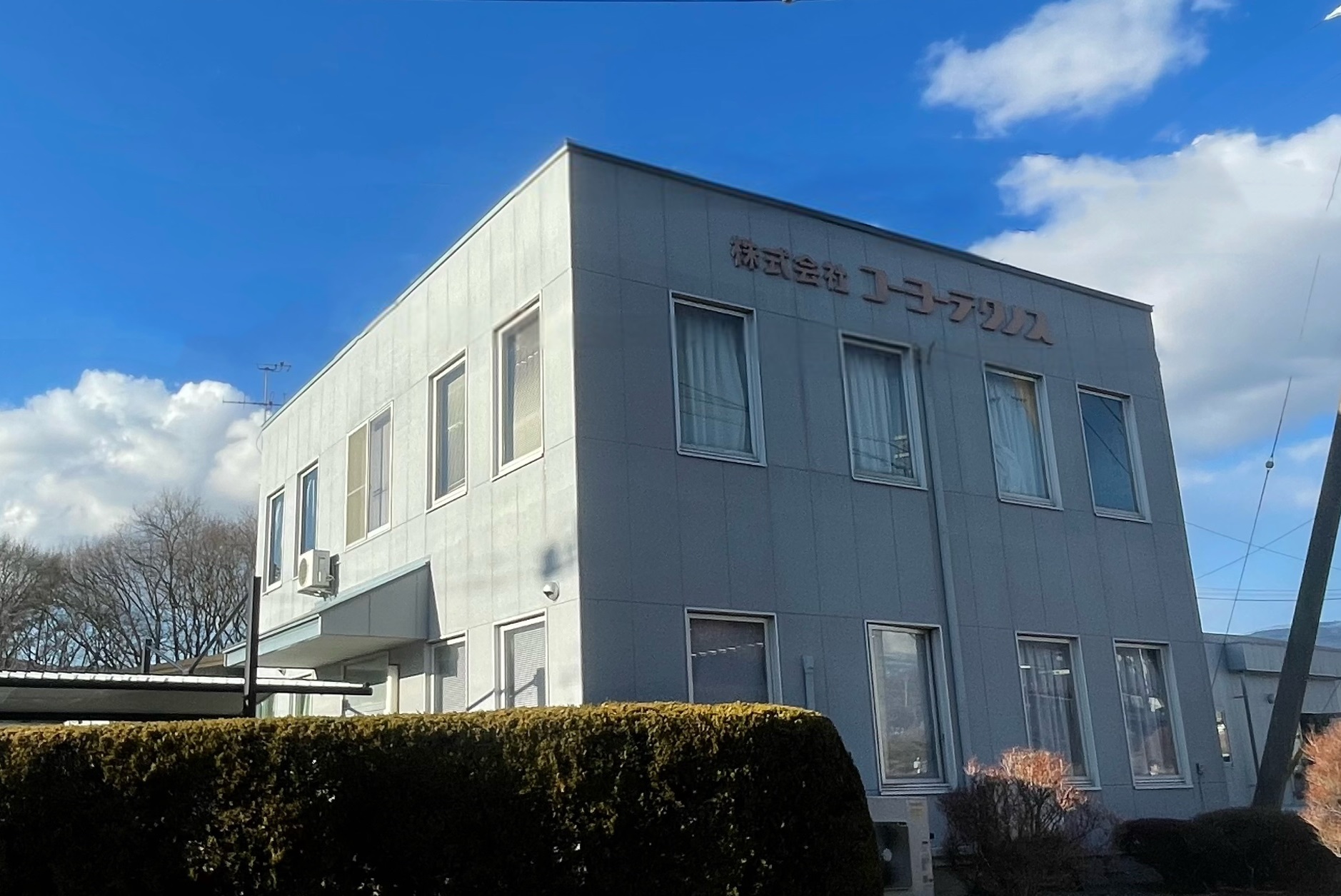
本社/本社工場/第一工場/第二工場:長野県茅野市豊平373
設立:1995年5月1日
資本金:5,000万円(2025年1月現在)
従業員数:73名(国内関連会社:52名・海外関連会社:81名)
事業内容:
・プリント基板・FPCの検査治具作成
・半導体・電子部品の検査治具作成
・プリント基板のテストサービス
・特殊便利治具の作成
株式会社コーヨーテクノスのサイトはこちら
現場力で回していた生産現場を見える化
事業戦略部 取締役部長 長尾積憲氏
「以前は生産を管理するという概念がなく、生産現場の状態が把握できないままで仕事を回していました」
新生産管理システムを導入する以前は、受注登録や納期設定まではシステム化されていました。
しかし、生産現場に受注情報が送られてからは、進捗状況、加工内容、所要時間を把握する手段がないので、生産の進捗は電話やホワイトボードを使って情報共有していました。
工程計画、進捗管理、作業実績のデータが集計されていないので生産効率の改善にも手が付けられないでいました。
生産状況を見える化することで、課題を解決し、ビジネスを定量的に把握し効率化するため、新生産管理システムの導入を決めました。
導入前に主な要件として挙げたのは2点です。
・工程・進捗の見える化(ガントチャートなどを使用)
・1時間単位での進捗確認
進捗確認については、通常は1日や1週間の単位で行うところですが、より細かく進捗を確認するために1時間単位としました。
既存のシステムは一切使わないことに決め、新生産管理システムへ一気にジャンプすることを決めました。
総務部 常務取締役総務部長兼経理部長 土橋賢太郎氏
「今、気にかかっていることは将来必ず問題として現れるので、そうなる前に改める必要があると思います」
新生産管理システムを導入する前は現場力で生産現場をなんとか回していましたが、データが残っていませんでした。
そのため、生産現場についてのファクトがわからず、分析と改善に手が付けられていませんでした。
私は、今は小さな引っかかりでも将来は大きな問題になり得るので、気になったら一歩踏み出して変える必要があると思っています。現状のやり方を変えることに不満が出るのは当たり前のこととして受け止め、企業としての最適解を求めるのが上層部の仕事です。
営業技術部 係長 小林大樹氏
「生産現場でどのくらい苦労して作ったのかがわからないので、価格を決めづらいという悩みがありました」
弊社の検査治具はお客様の基板や半導体に合わせて作るオーダー品です。それほど苦労せずに作れるものもあれば、非常に難しい設計が要求されるものもあります。
営業としては、難易度の高い製品には付加価値を反映した価格を設定したいのですが、生産現場でどのくらい苦労したのかが把握できないので、価格を付ける根拠が乏しくなってしまうという悩みがありました。
また、受注情報を登録すると後は生産現場におまかせだったので、納期は守れても品質や価格の面でお客様の要求を満たしているかどうかについても不安がありました。
社内承認から要件定義は、苦労の連続
総務部 常務取締役総務部長兼経理部長 土橋賢太郎氏
「生産設備と違って、情報システムの導入効果をなかなか理解してもらえませんでした」
新生産管理システムの導入の決裁を得るのは苦労しました。生産設備と違って効果が目に見えませんし、システムで仕事をすることにも不慣れなためです。
また、既存のシステムでも一応は仕事が回っていたので、新しくする必要性がなかなか理解してもらえません。
しかし、会社をより良くするためには、データを集めて分析し、改善策を議論することが必要だと押し切りました。
事業戦略部 取締役部長 長尾積憲氏
「業務フローを整理し、要求仕様をまとめて、約30社候補を検討しました」
新生産管理システム導入は決裁されましたが、いきなり開発を始めるのではなく、開発を始める前の検討プロジェクトをまず承認してもらいました。
システム導入までに予想されるさまざまなハードルを乗り越えるため、専任者として山岸と御子柴の2名を配置しました。彼らが業務フローを整理し、要求仕様をまとめました。
生産管理システムを提供している会社を約30社調べ、最終的に3社に要求仕様を送って提案をもらいました。
最終的にトーテックさんを導入パートナーに決定したのは、以下の理由からです。
1) 既存のシステムの機能をTPiCS-X標準パッケージでカバーしている。
2) 今後取り組みたい資材管理の機能がある。
3) SEの知識と対応が他のベンダーより優れている。
4) トーテック独自のイージーオーダー型テンプレート「PI-navi」でカスタマイズにも柔軟に対応できた。
・ 受注管理機能の実装
・ 1時間単位での進捗管理
トーテックとのコラボレーション
製造部 生産管理課 係長 山岸康弘氏
「現場の要望を実現するため、トーテックさんからさまざまな提案をいただきました」
私もパートナー選定に関わりましたが、トーテックさんを選ぶ決め手となったのは、技術力、柔軟性、弊社の仕事のやり方に合わせてシステムを作れると思えたことです。
他社の提案ではシステムに合わせて仕事のやり方を変える必要がありましたが、トーテックさんの提案はシステムを弊社のやり方に近づけるというものでした。
これなら実現可能だと判断し、実現性検討のフェーズに進みました。
最初に手を付けたのは要件定義です。以下のようなステップで進めました。
1) 現状確認
2) TPiCS-X標準機能説明
3) 課題、要望確認
4) Fit&Gap
5) PI-navi機能概要検討
6) システムフロー作成
要件定義を進める中で各部署の要望をどう実現するかをトーテックさんと検討しましたが、「できない」とは言わずに「どう実現するか」を考えました。
トーテックさんから「こんな方法はどうですか?」と提案をいただき、実現したことも多くあります。
製造部 生産管理課 御子柴聡一氏
「ゆるやかに新システムに移行するのではなく、一足飛びに変えたかったので念入りにテストしました」
既存のシステムから一足飛びに新生産管理システムに移行する計画だったので、業務を止めないように運用テストは念入りに行いました。
システム担当者がテストして問題を解決した後に生産現場でテストしてみると、新しい問題が見つかるということがありました。
このため、運用テストの回数を予定より増やして、仕事を止めずに運用できるという確信が得られるまで繰り返しました。問題解決が行き詰まったときは、トーテックさんから提案をもらいながら進めました。
実績入力は生産現場にとっては新しい業務なので、「実績を入力すると、どんなメリットがあるの?」という疑問が聞かれました。データを蓄積する意義を説明し、システムの使い方をマニュアル化して説明しました。
―― 使い方をわかりやすくまとめたマニュアル ――
緻密な運用テストにより、一足飛びのシステム導入が可能に(トーテック 鳥居浩樹)
産業システム事業部 鳥居浩樹
コーヨーテクノス様の要求仕様の件数がたくさんありましたが、実現できない項目はなかったので、整理して要件定義を作成しました。その要件定義をベースに山岸様と御子柴様が各部署にていねいに説明をされ、問題があれば、素早く対応されていました。
現場からの反発もあったと思いますが、なんとかして導入するという強い気持ちを感じました。
事前のテストでは解決できなかった問題も出ましたが、コーヨーテクノス様と協力して解決方法を考え、徐々に移行するのではなく、一足飛びに新生産管理システムに移行することができました
現場では反発も
製造部 製造1課 課長 伊藤尚武氏
「苦労はありましたが、今までルーズだった現場の意識が変わり、生産効率が上がりました」
私は生産現場で新生産管理システムを使う立場です。
以前は進捗、実績、歩留まり、稼働率などをあまり気にかけていなかったので、自由が利く反面、ルーズでもありました。
納期さえ守れればいいという風潮があり、生産性や歩留まりを上げるような取り組みはあまり見られませんでした。
ところが、新生産管理システムが導入され、実績、進捗、振り返り、実績管理などのデータで自分たちの仕事が客観的に見られるようになり、意識が変わってきました。
具体的な例を挙げると、作業時間の予測と実績が合うようになってきました。
ムダな時間があればわかりますし、作業員が持ち時間と自分の技量を考えて時間を配分するようになりました。
結果として、ムダな時間は減り、生産効率が上がりました。
単に指示どおりに作業するのではなく、作業員自らが考えて作業するようになり、指示する/されるだけの関係から抜け出せたことが意識改革につながったと思います。
それでも現場への導入には苦労しました。データを入力する習慣がなかったので、作業のたびにデータを入力することに対して反発がありました。
しかし、システム担当者が現場に出向いてシステム化の意義をていねいに説明し、問題があれば素早く修正していたので、現場とシステム担当者の間でうまく意思疎通ができていたと感じます。
これがスムーズに導入できた要因のひとつですね。
―― 生産現場で進捗状況を入力する ――
新生産管理システムを会社のインフラに
事業戦略部 取締役部長 長尾積憲氏
「生産管理だけでなく、業務のプラットフォームとして成長させる計画です」
当初の目標であった生産管理と受注管理は新生産管理システムで実現できました。
まだ、やるべきことは残っていますが、今後の方向としては資材管理機能を追加したいと思っています。
さらに在庫管理などの機能も加え、新システムを業務のプラットフォームとして活用したいと考えています。
総務部 常務取締役総務部長兼経理部長 土橋賢太郎氏
「データで経営判断するベースができあがりました」
新生産管理システムで集計したデータが蓄積され、ようやくデータをベースにした議論ができるようになったと感じています。経営判断の材料としても使えるようになりました。
現在気になっていることを手つかずにしておくと将来大きな問題になってしまうので、気が付いたら手を付けることが肝心です。
今回の新生産管理システムの導入は、会社の将来を考えたときに、今、手を付けておくべき案件です。
決裁承認で苦労しても、現場からの反発があっても、必ずシステム導入をやり遂げる気持ちでした。
新システムは会社の背骨となるインフラです。ここを太く、しっかりさせておくことが将来にわたって会社の成長を支えると思います。
取材日:2025年1月21日
記載の担当部署は、取材時の組織名です。
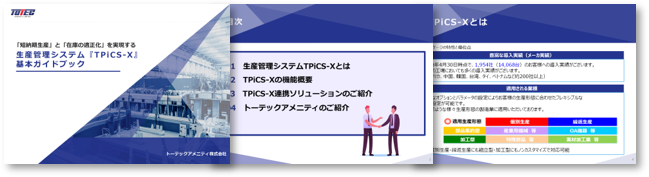
生産管理システム「TPiCSーX」
お困りごとがありましたら、お気軽にお問合せください。