工場の原価管理 ~原価低減のための仕組みづくり~
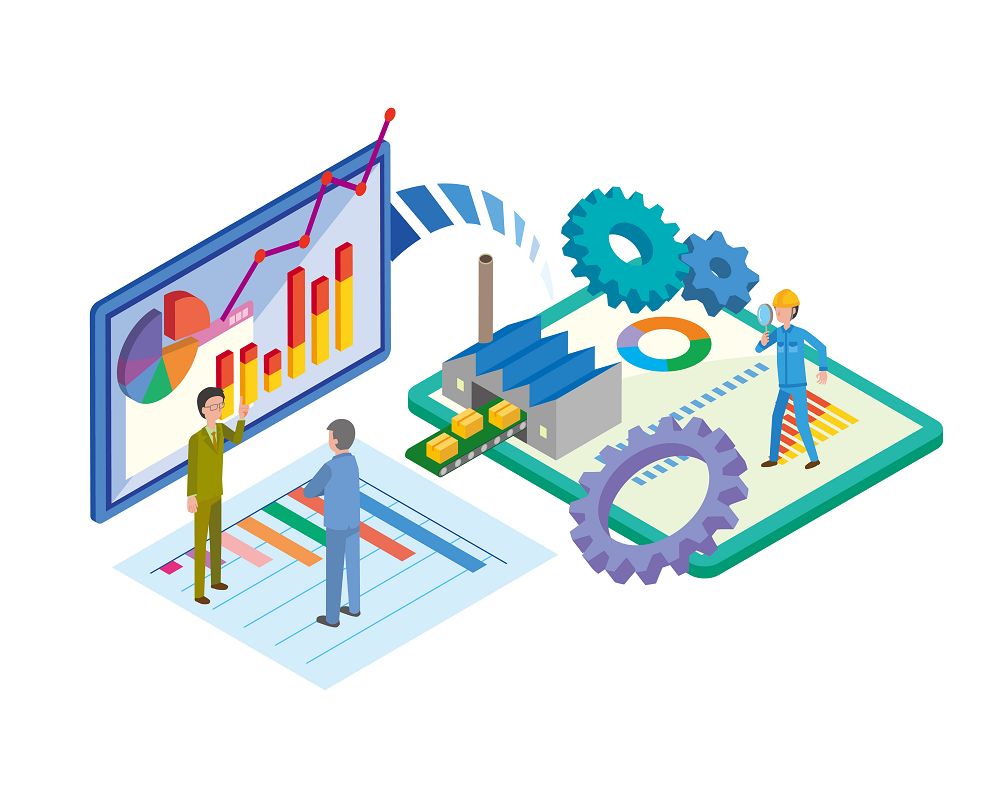
連載テーマ「生産管理システムを理解する」
- Vol.1 生産管理業務とは〜目的から基本原則まで〜
- Vol.2 生産管理システム~その機能、役割とは?どう選べばよいのか?~
- Vol.3 生産管理の基準情報(マスターデータ)の整備と維持~基準情報は会社のノウハウそのもの~
- Vol.4 生産計画と日程管理 ~生産管理システムにおける生産計画や日程計画の立案とは~
- Vol.5 在庫管理システムと生産管理 ~在庫管理の考え方と実践~
- Vol.6 資材発注・外注管理 ~社外への手配管理の内容と重点管理ポイントについて~
- Vol.7 製造管理~社内における作業管理と工場の統制~
- Vol.8 品質管理~生産管理システムと品質管理の関係~
- Vol.9 生産管理と受注出荷の連携 ~営業活動と工場との関係~
- Vol.10 工場の原価管理~原価低減のための仕組みづくり~
ものづくりを生業とする製造業である以上、原価管理をすることは避けて通れません。
商品を製造するのにいったいいくらかかっているのか、売価は適正なのか、利益は出ているのか。
こういった評価をするためには日々の生産活動の中に原価をとらえるための仕組みを組み込む必要があります。
今回は工場マネジメントとしての原価管理と生産管理システムの関係について解説します。
原価管理の目的
製造業における原価管理の定義は、「原価の標準を設定してこれを指示し、原価の実際の発生額を計算記録し、これを標準と比較して、その差異の原因を分析し、これに関する資料を経営管理者に報告し、原価能率を増進する措置を講ずること」とされています。
つまり、製造原価を下げて利益増大を図るためには、その原価構造を明らかにし標準値と比較することによって改善点を見つけ、対策することが必要ということです。
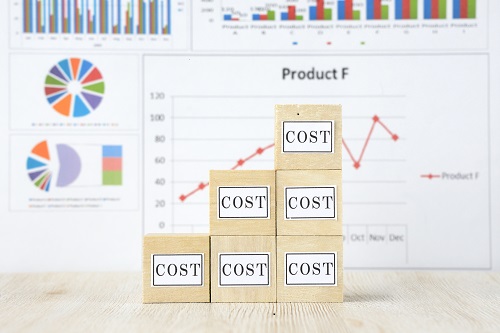
原価管理をしないとどうなるかというと、いわゆる「どんぶり勘定」になるわけです。
今月の売上は●●円でした。使ったお金は▲▲でした。従って利益は■■円でした。前月と比べて利益が下がっていますが、原因は不明です・・・。
これでは会社は成長できません。あるべき姿は、使ったお金の内訳を明確化し何にたくさん使ったのか、削れるところはないのか検討できるようになっていることです。
また工場マネジメントとしての原価管理は財務会計ではなく管理会計です。従ってどういう視点で、どういう原価計算を行えば原価改善が可能となるかは会社それぞれで異なりますので、経営ノウハウそのものと捉えることもできます。
原価管理の手順
原価管理は一朝一夕で出来るものではなく、手順を踏むことが必要です。以下にその手順を解説します。
⑴標準原価の設定
製造業における原価管理の考え方で一般的なのは、製品別原価です。製品を1つ作るのにいくらかかっているのかという尺度です。そこでまず、各製品別の標準原価を決めます。標準原価の決め方はその会社の考え方次第ですが、アプローチの種類として市場相場から決める場合と、製造コストの標準値を積み上げて計算する場合があります。
⑵原価計算
製造コストに関わるデータを集め、原価計算を行います。原価計算には大まかに下記の種類があります。
・標準原価計算
標準値による原価計算です。計画段階で実施し、予算策定や目標設定等に使用します。
・実際原価計算
実際に使われたコスト情報をもととする原価計算です。この計算により各製品1つあたり製造に実際いくらかかっているかが明らかになります。
・個別原価計算
個別受注生産品やプロジェクト等のように個別で収支を評価したい場合の原価計算です。
⑶原価差異分析
標準原価計算の結果と実際原価計算の結果を比較して差異がある場合はその原因を分析します。
当然ですが、最終結果の合計金額だけを比較しても原因はわかりませんから、その内訳、仕訳別に比較できないといけません。
⑷改善
原価差異分析の結果改善の余地がある箇所に対して対策を打ちます。対策を打った結果は効果が表れているかを次回の原価計算で確認します。
以上の手順を繰り返し実施することでいわゆるPDCAサイクルとなり、原価改善が進むということになります。
原価管理システムの構築
2.で述べたように原価管理の仕組みを確立するには手順を踏むことが必要です。しかし手順を理解したからと言ってすんなりできるわけではありません。ここではもう少し踏み込んで原価管理システムを構築するコツをお話ししたいと思います。
まず、生産の管理統制がきちんとできていることが前提となります。これは第8回の品質管理でも述べましたが、生産業務そのものが標準化され統一のルールにもとづいて遂行されている必要があります。
作業員それぞれが自分勝手な作り方をしているようでは原価計算をしたところで何が悪いのか、どう改善すればよいかわからないでしょう。実際原価のデータを取ったところでバラツキが大きかったりそもそも取り方が一定でなかったりして正しく計算できない場合が多いです。
次に、アウトプットと計算式を明確にするということです。計算式自体は中学校程度の数式ですので難しくないはずですが、難しいのは按分や割合の計算式の設定です。原価情報には、「全部でいくら」というコストが存在します。光熱費や管理費用等、目的別や製品別にできない費用が該当します。これらのコスト情報は一定のルールで按分(費用を分配すること)する必要があり、そのルールを計算式化しなければなりません。計算式ですので曖昧は許されず、ケースバイケースであれば全ケースを計算式として表現できなければなりません。
さて、直接原価計算するためには生産活動の実績コストをデータ化できる仕組みが必要です。原始的な方法としては日報に作業時間を記録する、というやり方がありますがそれを入力、集計するのは大変な作業です。理想的には生産管理システムを導入し、システムの中で実績データを収集できるような機能を組み込んでおき、原価計算式をコンピュータプログラム化しコンピュータで原価計算をしてしまうのが最良でしょう。コンピュータが計算しますので計算ミスはなく、計算にかかる時間も人力と比べれば比較にならないほど速くできるでしょう。
また、原価差異の分析にもコンピュータは不可欠です。例えばまず仕訳別で標準原価と実際原価を比較でき、差異が大きいところを深堀して費目別や明細で比較できる、といった分析作業(ドリルダウン分析)が素早くできる必要があります。そのためには計算の途中結果を保持でき、さまざまな切り口で集計出来たり深堀出来たりする機能が必要となります。また分析機能は最終的にその企業の原価管理に対するニーズに直結するものであるため、アウトプットを明確にしておく必要があります。
原価管理システムの構成
原価管理をコンピュータシステム化する場合、管理会計ということもあり経験上ほとんどのケースでスクラッチ開発(手づくり)となります。実装する機能としては以下のものが挙げられます。
①マスターデータ整備機能
原価計算のためのマスタデータを登録する機能です。標準原価情報や組織情報、設備情報、費目情報などを登録します。
②原価情報収集機能
実績原価を計算するためのデータを収集し蓄積する機能です。直接原価情報は生産実績や設備稼働実績と連動して収集し、間接原価情報はインポートやダウンロードなどにより取り込めるようにします。
③原価計算機能
原価計算を行う機能です。各種のインプットデータから計算式に従って計算結果を画面や紙面に出力します。
④原価分析機能
原価計算の結果を掘り下げてアウトプットし、原価差異の分析を行う機能です。
生産管理システムや生産計画システムはいわゆる「パッケージソフト」製品が多数リソースされていますが、原価管理システムにはそういったパッケージソフトはあまり見当たりません。たとえあったとしても自社に合わないところがどうしても出てきますので結果的に使えないケースが多いからだと思います。
まとめ
工場の原価管理を実現するにはまず統制の取れた生産管理が必要であり、そのうえで原価改善に繋げられる原価計算、原価差異分析の仕組みが必要です。一定のルールで生産活動が行われることで初めて標準原価が意味を成し、標準に沿ったオペレーションで生産を実行することで実績原価と標準原価の比較が改善に繋がります。原価管理をシステム化する際はアウトプットや分析方針を明確にし、全ての計算式が準備できるよう十分な検討を重ねることが大切です。
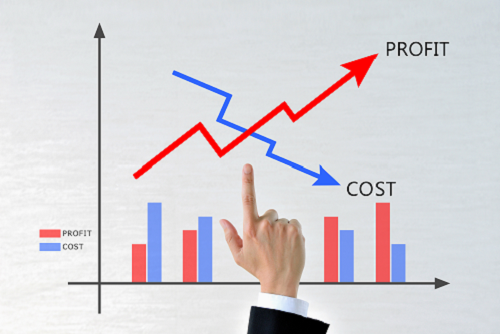
さて、これまで10回にわたって生産管理システムを解説してきましたが、今回で最終回となります。生産管理システムの導入を検討されている皆様にとって少しでも参考になれば幸いです。お付き合いいただきありがとうございました。
筆者
プロフィール
星野拓 Takumi Hoshino
経歴:
自動車部品メーカーの設備技術者、物流システムメーカーのSEを経てトーテックアメニティに入社。
生産管理システムのプレSE及びプロジェクトマネージャとして豊富な導入実績を持つ。
第1種情報処理技術者
IoTエキスパート
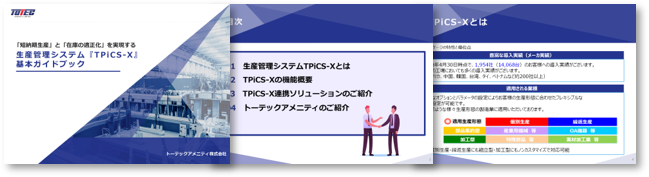
生産管理システム『TPiCS-X』
基本ガイドブック
お困りごとがありましたら、お気軽にお問合せください。