製造管理~社内における作業管理と工場の統制~
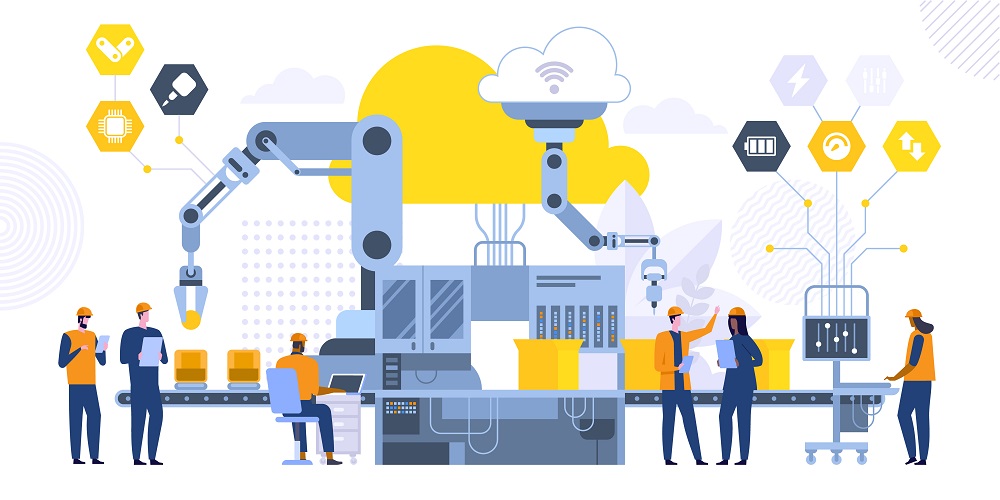
連載テーマ「生産管理システムを理解する」
- Vol.1 生産管理業務とは〜目的から基本原則まで〜
- Vol.2 生産管理システム~その機能、役割とは?どう選べばよいのか?~
- Vol.3 生産管理の基準情報(マスターデータ)の整備と維持~基準情報は会社のノウハウそのもの~
- Vol.4 生産計画と日程管理 ~生産管理システムにおける生産計画や日程計画の立案とは~
- Vol.5 在庫管理システムと生産管理 ~在庫管理の考え方と実践~
- Vol.6 資材発注・外注管理 ~社外への手配管理の内容と重点管理ポイントについて~
- Vol.7 製造管理~社内における作業管理と工場の統制~
- Vol.8 品質管理~生産管理システムと品質管理の関係~
- Vol.9 生産管理と受注出荷の連携 ~営業活動と工場との関係~
- Vol.10 工場の原価管理~原価低減のための仕組みづくり~
ファブレス企業を除いて製造業の主戦場は自社工場です。今回は工場における製造管理とITの活用について解説します。
作業指示の出し方
一般的な生産管理システムを導入していれば、所要量計算等によって何をいつまでにいくつ作ればよいかはコンピュータが計算してくれます。
生産計画のアウトプットは通常作業指示書や製造指示書などの伝票に表現されますから、あとは出てきた伝票通りにモノ作りをすれば万事快調となるわけですがこれがそう簡単な話ではありません。
現実世界を考えてみましょう。
よほど小さな工場ならともかく、繰り返し生産の量産品の工場であれば、1日に発行される指示書の枚数は如何程のものでしょうか。
その伝票の束を現場に渡せば指示通りに製造してくれるでしょうか。
本ブログ4回目で述べたような“APS”やスケジューリングシステムがあれば別ですが、そうでなければ伝票を現場に渡す前に「捌き」が必要になることは容易に想像がつきます。
つまり、工場を管理するスタッフが各工程に対して今日はこれとこれと・・・をやってください、のように細かい指示とともに指示書を渡してあげることが工場を円滑に運用するために必要になってきます。
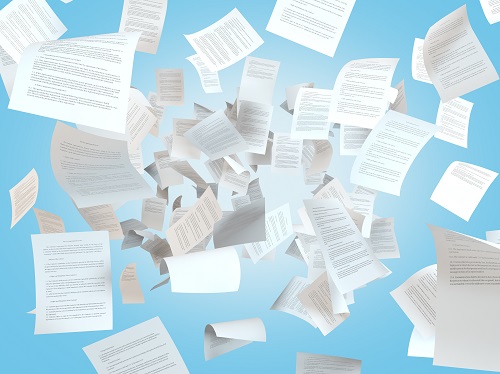
もっと言うと、工場を円滑に回すには作業の順番や組み合わせなども影響するかもしれません。単純に納期の早い順ではなく、最終的に納期遅延が起こらないように滞留や待ちが発生しない作業の順番を考えなくてはなりません。
また人や設備の割り当てに無駄が発生しないという視点も必要です。
さて、一般的な生産管理システムの計画のアウトプットは伝票であると言いましたが、紙の伝票は「捌き」と「配布」に時間がかかります。
これをペーパーリードタイムと言います。
ペーパーリードタイムは物理要因に影響されやすく、発行する伝票の枚数が多ければ多いほど、また工場が広ければ広いほどペーパーリードタイムは長くなります。
せっかくシステムがジャストインタイムで伝票を発行してもそれを現場に配るのが遅ければジャストインタイムでモノづくりができません。
ペーパーリードタイムを無くすには、早い話が紙を無くしてしまえばいいわけです。
システムが計画を作ったら、紙に出さずにコンピュータの画面上で「捌き」をやってしまいます。そして各工程に対して作業割当と順番を決めたら、各工程に設置した端末の画面上に表示してあげます。各工程の作業者は画面を見て指示された順番に作業をします。
近年では工場のWiFi化が進み、タブレット端末の普及とともにこういった仕掛けも作りやすくなっています。
手作業が主体の物流現場ではもっと進んでいて、作業者が装着したウェアラブルデバイスに直接指示が表示される、なんていう近未来的なモノも登場しており、マンガの世界そのままに「スカウター」と呼ばれています。
作業実績の収集
さて、製造指示書が発行され現場では指示書に従い作業を行ったら、作業が終わった証を残さなくてはなりません。
コンピュータシステムがない場合は指示書に「済」のハンコを打つとか、出来高と終了日、氏名を記入して保管したりするでしょう。
生産管理システムを導入している場合、これらの行為に代わるものが「実績のインプット」です。
コンピュータに、どの指示に対して、いつ、だれが、何をいくつ作ったかを入力します。
これにより、コンピュータはどの指示が終わっていてどれが終わっていない、どこまで進んでいる等の進捗を把握することができます。
また在庫の変動が伴う場合はどの材料や部品がどれだけ消費され、かわりにどの製品がいくつできたかの在庫情報の更新も同時に行われます。
結局のところ、コンピュータで指示を出したのであればコンピュータへの実績情報のインプットは必須です。
ところが、これが現場においてはなかなか受け入れられないことが多いのが実情です。
元来、現場で働く方々はITが苦手な方が多いのは事実です。
最近は皆がスマホを持っているためITへのアレルギーもだいぶ少なくなりましたが、昔はコンピュータを前にして固まってしまう人が多かったものです。
こういう仕組みは現場に受け入れられなければアウトですので、今でも現場に端末を置く場合は画面デザインに細心の注意を払います。
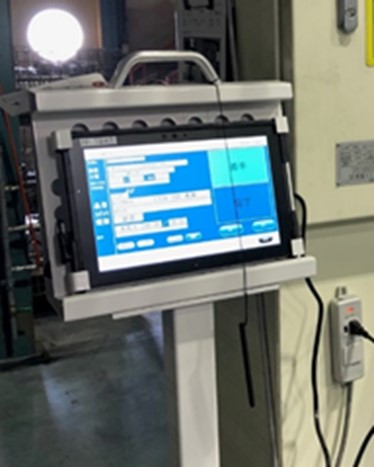
作業実績収集をシステム化するときは、ユニバーサルデザインも大事ですが何を入力させるかの検討も重要です。
作業指示の消込だけであれば伝票番号と出来高だけで良いですが、進捗を見たければ着手記録も必要ですし後で原価集計をしようとするなら段取にかけた時間等も必要になります。
そもそも現場の人にとって実績入力はモノづくりに関係ないムダな作業ですから、そこを曲げて入力をしてもらうにはなぜ実績入力が必要か、それで何が良くなるかを前もってきちんと説明して協力をとりつける必要があります。
また入力項目が増えるとそれだけアレルギー症状も出やすくなるため、項目の要否は慎重に検討する必要があります。
作業進捗の管理
作業指示を出したら、実績が入力され完了するまで進捗を管理しなければなりません。
出荷する製品はいってみれば作業指示の集まりで出来ているので最終的に納期遅延を起こさないためには全ての作業が予定通りに進まないといけません。
第4回目でも書きましたが、基本的にシステムは納期に「遅れそう」という状況は判別できません。
自動加工機のカウンターのように出来高がカウントアップされていけば遅れそうかどうかわかりますが、生産管理システムへの出来高インプットはその作業が完了するか、直の交代時のような区切りで入力することが殆どで、遅れたか遅れなかったかの判断がやっとです。
基本的にはマスターを適正化し、適正なリードタイムを与えれば納期は守れる状態を作ることが大切です。
それでも途中経過を見えるようにしたければまずは着手記録を採り、IoT技術などを活用して設備から自動的に実績データを採ることを考える必要があります。
膨大な作業指示を、遅れがないかどうかを確認するのは大変な作業でここはITに頼るべきところです。
紙をチェックするのではなくデータをチェックすれば納期遅れしている作業指示を割り出すことは簡単にできますし、ガントチャート等の視覚ツールを使えば一目で遅れが分かるようにできます。
色でアラームを表現したり、メールで遅れを通知することであんどんの役目を電子化することも可能となります。
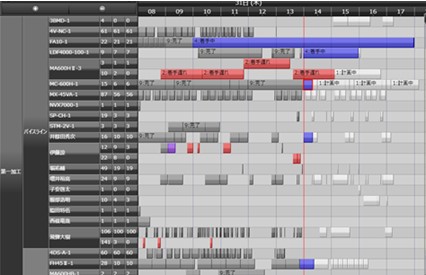
IoTはどこまで使えるか
最近、IoTを工場へ応用した「工場IoT」という言葉をよく聞きます。
よくあるのが、「工場IoTを導入して実績を自動で採りたい」という要望です。
IoTはもともと身の回りにある「モノ」(多くは工業製品)をインターネットにつなげてオンラインで活用しようという思想を言いますが、工場IoTは工場内にある設備をネットワークに繋げて自動化を推進しようというものです。
IoTという流行りの言葉を使ってはいますが、要はFA(FACTORY AUTOMATION)のことです。
確かに今日ではネットワークにそのまま接続できる工作機械は増えましたが、工場にある機械がなんでもかんでもネットに繋げるというわけではありません。
まず接続可能なインターフェースを持っていることが必要です。
NC工作機やPLC等はネットワークインターフェースを標準装備していることが多いですが、有人工作機械やオーダーメイドの専用機の場合はそういったインターフェースを持っていないことが多くそのままでは繋げられません。
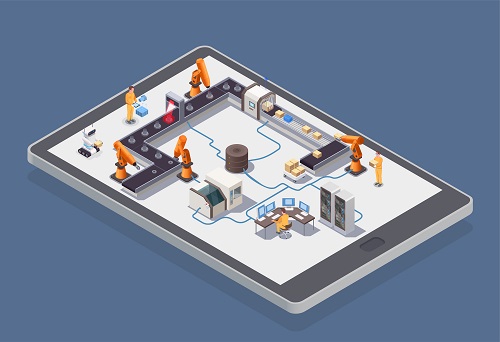
PLCを介すか、制御部分をNCに置き換えるなどの改造が必要になります。
また、どういった情報がやり取りできるかはその機械の制御部がどれくらいインテリジェントかで決まります。
メイン電源とスタートスイッチ、ストップスイッチしかない機械は稼働時間くらいしか取れませんし、単純な順送プレスであれば、それに加えてショット数がせいぜいでしょう。
これでは生産管理システムの実績収集には使えません。生産管理システムが欲しいのは「どの指示に対してか」なのです。
指示番号をやり取りできてこそ、終わった指示の消込ができ、進捗が管理できるのです。
いくら出来高や稼働時間が取れても、どの指示に対しての実績かが分からないとどうしようもないのです。
結論としては、生産管理システムの実績収集においてIoTが成り立つのは「指示番号」がやり取りできる設備、ということになります。
例としてFMS、MES、SCADA等のCPUを持った設備やNC工作機械が挙げられるでしょう。
これらは指示番号を「オーダー」として受取り、仕事が終わったら終了を返してくる、という動作をします。工場の設備が全てこれらに当てはまるならIoTを進めるべきですが、そうでないならIoTは妄想の域を出ることはありません。
まとめ
作業指示を的確に出し、実績をもとに進捗管理することは工場の統制に欠かせない業務です。
それにより工場が安定稼働することで現場の信頼も得られ、あらゆる改善活動がやりやすくなっていきます。
工場が大きくなればなるほど膨大な情報との戦いになりますので使えるITは積極的に活用しましょう。
情報の収集、仕分、集約、アウトプットはITに任せ、人はより付加価値のある仕事に専念できる環境を整えることが重要だと考えます。
現場に追われることが生産管理マンの仕事ではないのです。
筆者
プロフィール
星野拓 Takumi Hoshino
経歴:
自動車部品メーカーの設備技術者、物流システムメーカーのSEを経てトーテックアメニティに入社。
生産管理システムのプレSE及びプロジェクトマネージャとして豊富な導入実績を持つ。
第1種情報処理技術者
IoTエキスパート
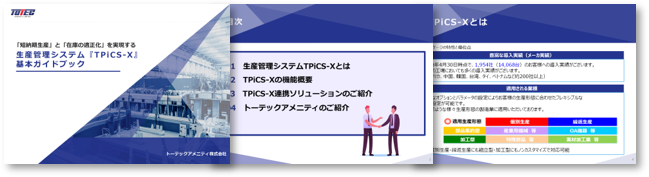
生産管理システム『TPiCS-X』
基本ガイドブック
お困りごとがありましたら、お気軽にお問合せください。